Water turbine sleeve casting mould assembling box
A water turbine and sleeve technology, applied in the direction of mold box, mold, mold composition, etc., can solve the problems of blocked sand core exhaust, unstable molten iron flow, and no shrinkage, shrinkage and cracks in castings. Easy to shape, reasonable structure, reduce the effect of local overheating
- Summary
- Abstract
- Description
- Claims
- Application Information
AI Technical Summary
Problems solved by technology
Method used
Image
Examples
Embodiment Construction
[0009] In order to deepen the understanding of the present invention, the present invention will be further described below in conjunction with the embodiments and accompanying drawings. The embodiments are only used to explain the present invention and do not constitute a limitation to the protection scope of the present invention.
[0010] Such as figure 1 Shown is an embodiment of the casing of the hydraulic turbine sleeve casting mold of the present invention, including a sand box 1, a sand mold 5 is evenly arranged inside the sand box 1, a casting 2 is arranged inside the sand box 1, and an annular riser is arranged on the upper end of the casting 2 An air outlet 4 is provided between the mouth 3, the riser 3 and the upper end of the sand box 1, and a sand core 5 is provided through the air outlet 4, the riser 3, and the casting 2, and the upper end of the sand core 5 is placed outside the sand box 1, and the sand The lower end of the core 5 passes through the casting 2 a...
PUM
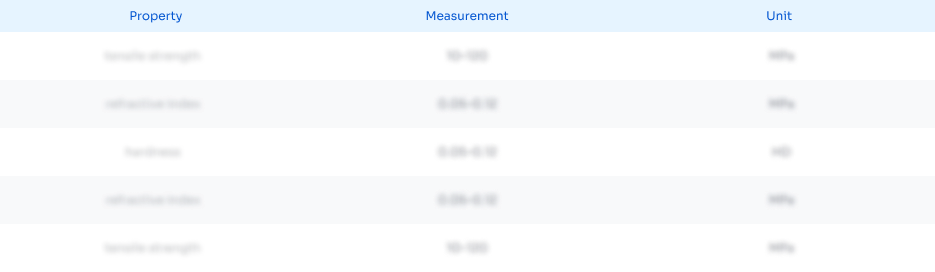
Abstract
Description
Claims
Application Information

- R&D Engineer
- R&D Manager
- IP Professional
- Industry Leading Data Capabilities
- Powerful AI technology
- Patent DNA Extraction
Browse by: Latest US Patents, China's latest patents, Technical Efficacy Thesaurus, Application Domain, Technology Topic, Popular Technical Reports.
© 2024 PatSnap. All rights reserved.Legal|Privacy policy|Modern Slavery Act Transparency Statement|Sitemap|About US| Contact US: help@patsnap.com