Non-contact dynamic torque, rotating speed and shaft power signal transducer
A signal sensor, dynamic torque technology, applied in instruments, power measurement, torque measurement, etc., can solve problems such as unfavorable mechanical system application, bulky, complex mechanism, etc., to improve mechanical transmission efficiency, small size, and improve intelligence. Effect
- Summary
- Abstract
- Description
- Claims
- Application Information
AI Technical Summary
Problems solved by technology
Method used
Image
Examples
Embodiment Construction
[0047] Below in conjunction with accompanying drawing, the present invention will be further described by embodiment:
[0048] combined with Figure 5 And attached Figure 7 A non-contact dynamic torque, speed and shaft power sensor with two signal receivers is described based on the improved plum blossom flexible coupling. Firstly, make a relational chart of the static torque of the coupling and the relative displacement between the active half and the passive half, and input the relational table into the first data processor of the signal processing circuit as basic data. When the driving shaft rotates and drives the driven shaft to rotate through the flexible coupling, when the driven shaft is unloaded, the torque is zero (or close to zero), the relative displacement between the two coupling halves is zero, and the two signal receivers from The signal test points obtain fluctuating signals respectively, and the two signals are amplified, shaped and phase-compared by the s...
PUM
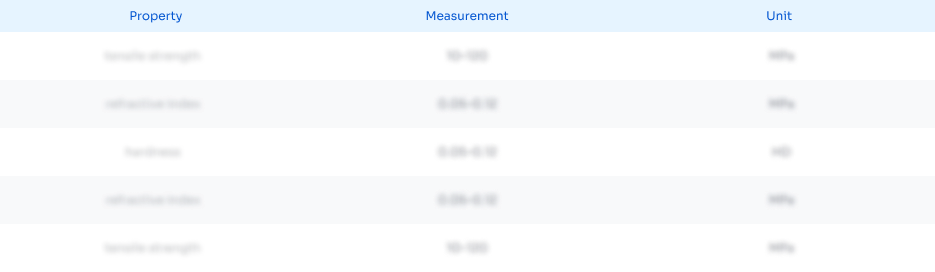
Abstract
Description
Claims
Application Information

- R&D Engineer
- R&D Manager
- IP Professional
- Industry Leading Data Capabilities
- Powerful AI technology
- Patent DNA Extraction
Browse by: Latest US Patents, China's latest patents, Technical Efficacy Thesaurus, Application Domain, Technology Topic, Popular Technical Reports.
© 2024 PatSnap. All rights reserved.Legal|Privacy policy|Modern Slavery Act Transparency Statement|Sitemap|About US| Contact US: help@patsnap.com