Assembling and splicing installation method of large-span tube-truss roof beam
An installation method and roof beam technology, applied in the processing of building materials, construction, building construction, etc., can solve the problems of high safety risks and difficult control of the space size of pipe truss roof beams, so as to reduce safety risks and save large machinery Cost, the effect of improving the mounting accuracy
- Summary
- Abstract
- Description
- Claims
- Application Information
AI Technical Summary
Problems solved by technology
Method used
Image
Examples
Embodiment Construction
[0026] In this embodiment, in the installation site of the pipe truss roof beams, firstly, the long-span pipe truss roof beams to be erected are divided according to the distance between the triangular steel column supports at both ends of the site and the concrete support columns in the middle Two spans of 75 meters are the left span of the roof beam and the right span of the roof beam; corresponding to the width of the concrete support column, the span of the middle span of the roof beam is designed to be 7.5 meters, forming a 75m+7.5m+75m Tube truss roof beams.
[0027] Since the spans of the left and right spans of roof beams are relatively large, in order to facilitate loading and transportation, the left spans of roof beams and the right spans of roof beams can be divided into three subsections (see figure 1 ), and made into sections in the factory. Since the span of the middle span of the roof beam is relatively small, it can be completed through overall fabrication, o...
PUM
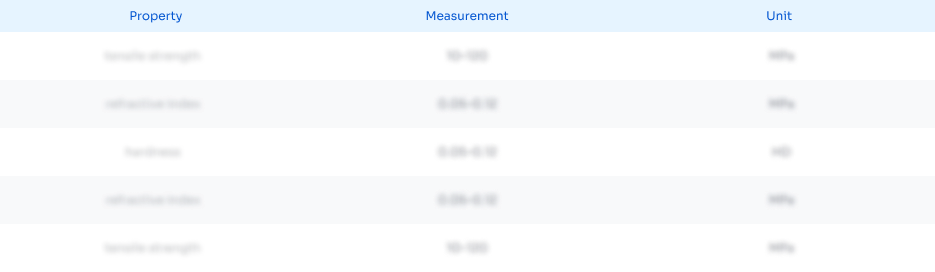
Abstract
Description
Claims
Application Information

- R&D Engineer
- R&D Manager
- IP Professional
- Industry Leading Data Capabilities
- Powerful AI technology
- Patent DNA Extraction
Browse by: Latest US Patents, China's latest patents, Technical Efficacy Thesaurus, Application Domain, Technology Topic, Popular Technical Reports.
© 2024 PatSnap. All rights reserved.Legal|Privacy policy|Modern Slavery Act Transparency Statement|Sitemap|About US| Contact US: help@patsnap.com