Quick pressing method for bamboo skin plywood and laminated wood
A technology of plywood and laminated timber, which is applied in the direction of manufacturing tools, wood processing appliances, and the joining of wooden veneers, can solve the problems of difficulty in promotion, increased investment in cold presses, etc., to reduce deformation and damage, reduce energy consumption, The effect of increased service life
- Summary
- Abstract
- Description
- Claims
- Application Information
AI Technical Summary
Problems solved by technology
Method used
Image
Examples
Embodiment 1
[0037] Choose bamboo strips and bamboo mats with a width of 2-3cm and a thickness of 1.2-2.0mm, and dry them to a moisture content of 8%. The material was soaked in a phenolic adhesive with a solid content of 25% for 5 minutes, removed, drained, and further dried to a moisture content of 15%. Design sheet density 0.9g / cm 3 , thickness 6mm, weighed after calculation, pave the bamboo mat on the outermost layer, and pave the bamboo curtain in the orthogonal direction according to the principle of symmetry, see image 3 ; Put into a hot press, the thickness is controlled by a thickness gauge. Control according to the following process parameters: the hot pressing temperature is 150°C, the high pressure pressure is 3MPa for 3min; the pressure is released to 2MPa within 30s, and the pressure is kept for 2min; the pressure is released to 1MPa within 30s for 4min, and the pressure is released to 0 within 1min to open the press. , take out the board, and store it after trimming (such...
Embodiment 2
[0039] Choose bamboo strips and bamboo mats with a width of 2-3cm and a thickness of 1.2-2.0mm, and dry them to a moisture content of 8%. The material was soaked in a phenolic adhesive with a solid content of 25% for 5 minutes, removed, drained, and further dried to a moisture content of 15%. Design sheet density 0.9g / cm 3 , the thickness is 12mm, weighed after calculation, the bamboo mat is paved on the outermost layer, and the bamboo curtain is paved in the orthogonal direction according to the principle of symmetry, see image 3 ; Put into a hot press, the thickness is controlled by a thickness gauge. Control according to the following process parameters: hot pressing temperature 150℃, high pressure 4MPa for 8min; pressure relief to 2MPa within 40s and hold for 2min; then pressure relief to 1MPa within 40s and hold for 4min; pressure relief to 0 within 3min to open the press , take out the board, and store it after trimming (such as image 3 ). Measured elastic modulus>...
Embodiment 3
[0041] Select bamboo strips with a width of 2-3cm and a thickness of 1.2-1.8mm, and dry them to a moisture content of 8%. The material was soaked in a phenolic adhesive with a solid content of 27% for 8 minutes, removed, drained, and further dried to a moisture content of 12%. Design sheet density 1.0g / cm 3 , the thickness is 25mm, weighed after calculation, all the bamboo curtains are paved in the forming frame in the same direction, put into the hot press, and the thickness is controlled by the thickness gauge. Control according to the following process parameters: hot pressing temperature 150℃, high pressure 5MPa, hold for 15min, depressurize to 2MPa and hold for 3min, then depressurize 1MPa for 2min, finally depressurize to 0 within 5min, open the press, take out the plate and store it .
PUM
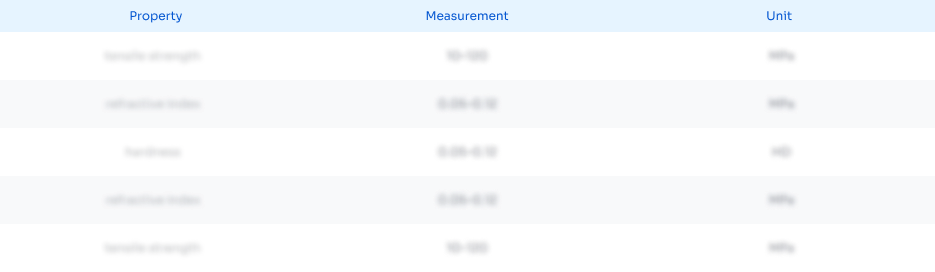
Abstract
Description
Claims
Application Information

- R&D
- Intellectual Property
- Life Sciences
- Materials
- Tech Scout
- Unparalleled Data Quality
- Higher Quality Content
- 60% Fewer Hallucinations
Browse by: Latest US Patents, China's latest patents, Technical Efficacy Thesaurus, Application Domain, Technology Topic, Popular Technical Reports.
© 2025 PatSnap. All rights reserved.Legal|Privacy policy|Modern Slavery Act Transparency Statement|Sitemap|About US| Contact US: help@patsnap.com