Method and device for controlling ink droplet drying process of inkjet printer
A technology of inkjet printer and drying process, applied in the direction of printing device, printing, etc., which can solve the problems of impact, unfavorable device performance, etc.
- Summary
- Abstract
- Description
- Claims
- Application Information
AI Technical Summary
Problems solved by technology
Method used
Image
Examples
Embodiment Construction
[0019] In the present embodiment, the method for controlling the drying process of ink droplets for the inkjet printer is to set a pair of flat electrodes to form a uniform electric field between the flat electrodes. The surfaces are perpendicular to each other, so that the surface of the printing substrate 3 is induced or polarized to generate surface charges, and the Coulomb force between the surface charges of the printing substrate and the solute molecules and solvent molecules in the ink controls the spreading of ink droplets on the printing substrate , solvent evaporation and solute film formation process.
[0020] see figure 1 and figure 2 , the structure of the ink drop drying process control device in this embodiment is set as:
[0021] A pair of flat plate electrodes is composed of an upper electrode plate 2 and a lower electrode plate 4. The upper electrode plate 2 is fixedly arranged on the bottom of the ink cartridge 1 and moves with the ink cartridge 1; the up...
PUM
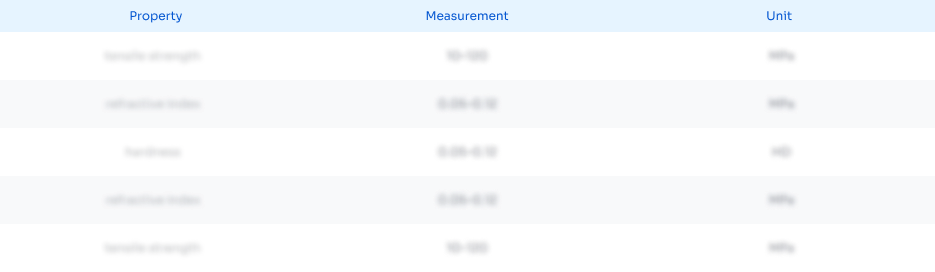
Abstract
Description
Claims
Application Information

- R&D
- Intellectual Property
- Life Sciences
- Materials
- Tech Scout
- Unparalleled Data Quality
- Higher Quality Content
- 60% Fewer Hallucinations
Browse by: Latest US Patents, China's latest patents, Technical Efficacy Thesaurus, Application Domain, Technology Topic, Popular Technical Reports.
© 2025 PatSnap. All rights reserved.Legal|Privacy policy|Modern Slavery Act Transparency Statement|Sitemap|About US| Contact US: help@patsnap.com