Method for preparing photoelectric composite submarine cable
A submarine cable, optoelectronic composite technology, applied in the manufacture of cables/conductors, insulation of conductors/cables, circuits, etc., can solve the problems of cable mechanical performance decline, poor aluminum waterproof effect, unable to guarantee the service life of submarine cables, etc. Guarantees the effect of water blocking performance
- Summary
- Abstract
- Description
- Claims
- Application Information
AI Technical Summary
Problems solved by technology
Method used
Image
Examples
Embodiment 1
[0045] A method for preparing a photoelectric composite submarine cable, characterized in that the following steps are adopted:
[0046] A), wire drawing treatment is carried out to the conductor;
[0047] B), utilize 91 coil frame winches to manufacture the conductor obtained in step 1 into three sections with a cross-sectional area of 630mm 2 round conductors;
[0048] C), the outer layers of the three circular conductors obtained in step B) are all wrapped with semi-conductive tape, and then the wires are respectively taken up to the 10m diameter transfer turntable through the steering guide wheel;
[0049] D) Pass the conductors on the three 10m-diameter transfer turntables through the vertical cross-linking production line VCV respectively to perform conductor shielding, insulation and insulation shielding co-extrusion processes, and perform water-blocking tape at the outlet of the vertical cross-linking production line VCV Spiral wrapping;
[0050] E), then the thre...
Embodiment 2
[0060] A method for preparing a photoelectric composite submarine cable, characterized in that the following steps are adopted:
[0061] A), wire drawing treatment is carried out to the conductor;
[0062] B), utilize 91 coil frame winches to manufacture the conductor obtained in step 1 into three sections with a cross-sectional area of 630mm 2 round conductors;
[0063] C), the outer layers of the three circular conductors obtained in step B) are all wrapped with semi-conductive tape, and then the wires are respectively taken up to the 10m diameter transfer turntable through the steering guide wheel;
[0064] D) Pass the conductors on the three 10m-diameter transfer turntables through the vertical cross-linking production line VCV respectively to perform conductor shielding, insulation and insulation shielding co-extrusion processes, and perform water-blocking tape at the outlet of the vertical cross-linking production line VCV Spiral wrapping;
[0065] E), then the thre...
Embodiment 3
[0075] A method for preparing a photoelectric composite submarine cable, characterized in that the following steps are adopted:
[0076] A), wire drawing treatment is carried out to the conductor;
[0077] B), utilize 91 coil frame winches to manufacture the conductor obtained in step 1 into three sections with a cross-sectional area of 630mm 2 round conductors;
[0078] C), the outer layers of the three circular conductors obtained in step B) are all wrapped with semi-conductive tape, and then the wires are respectively taken up to the 10m diameter transfer turntable through the steering guide wheel;
[0079] D) Pass the conductors on the three 10m-diameter transfer turntables through the vertical cross-linking production line VCV respectively to perform conductor shielding, insulation and insulation shielding co-extrusion processes, and perform water-blocking tape at the outlet of the vertical cross-linking production line VCV Spiral wrapping;
[0080] E), then the thre...
PUM
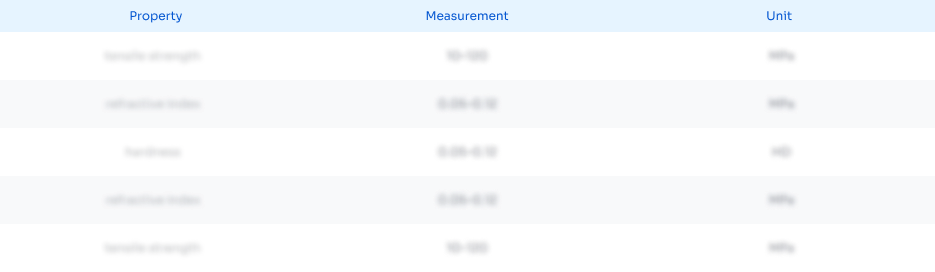
Abstract
Description
Claims
Application Information

- Generate Ideas
- Intellectual Property
- Life Sciences
- Materials
- Tech Scout
- Unparalleled Data Quality
- Higher Quality Content
- 60% Fewer Hallucinations
Browse by: Latest US Patents, China's latest patents, Technical Efficacy Thesaurus, Application Domain, Technology Topic, Popular Technical Reports.
© 2025 PatSnap. All rights reserved.Legal|Privacy policy|Modern Slavery Act Transparency Statement|Sitemap|About US| Contact US: help@patsnap.com