Double-end combined cutting machine
A cutting machine and integrated technology, applied in metal sawing equipment, sawing machine equipment, metal processing equipment and other directions, can solve the problems of reduced work efficiency, interruption of cutting process, trouble, etc., and achieve the effect of enriching the structure.
- Summary
- Abstract
- Description
- Claims
- Application Information
AI Technical Summary
Problems solved by technology
Method used
Image
Examples
Embodiment 1
[0027] Example 1: Please refer to Figure 1 to Figure 4 , the present invention comprises a frame 1, a frame foot 1A, a workbench 2, a rotating shaft 3, a longitudinal axis 4, a power head 5, a box 6, a relief groove 7, a blanking hole 8, a discharge guide groove 9, a saw Sheet 10, corner plate 11, positioning seat 12, adjusting screw 13, corner screw seat 14, corner screw 15, corner nut 16, corner handwheel 17, plane compression screw 18, plane compression screw relief groove 19, plane pressure Tight hand wheel 20, bearing 21, swing arm 22, feed cylinder 23, motor 24, motor shaft 25. The corner device and plane pressing device of this embodiment are manual structures, the bottom of the frame 1 is supported by the frame feet 1A and supports the workbench 2 upwards, and the two rotating shafts 3 are divided into left and right sides in the direction of the longitudinal axis 4. It is placed on the rear lower part of the box 6 added at the rear of the workbench 2 in a ground and...
Embodiment 2
[0028] Example 2: Please refer to Figure 5 to Figure 8 , the present invention comprises a frame 1, a frame foot 1A, a workbench 2, a rotating shaft 3, a longitudinal axis 4, a power head 5, a box 6, a relief groove 7, a blanking hole 8, a discharge guide groove 9, a saw Sheet 10, corner plate 11, positioning seat 12, adjustment screw 13, plane pressing screw relief slot 19, support 21, swing arm 22, feed cylinder 23, motor 24, motor shaft 25, corner cylinder 26, plane pressure Tightening screw 27, cylinder block 28, rotation compression cylinder 29, compression pin 30, compression surface 31, main shaft 32, motor shaft pulley 33, main shaft pulley 34, belt 35. The corner device and the rotary pressing device of the present embodiment are pneumatic structures, and the corner cylinder 26 acts on the upper part of the corner plate 11 with the box 6 as a fulcrum, and the plane pressing screw 27 passes through the plane pressing screw give way groove 19 to float and press. The c...
PUM
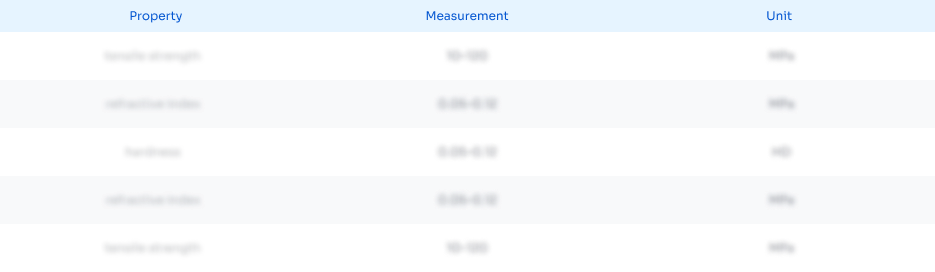
Abstract
Description
Claims
Application Information

- R&D Engineer
- R&D Manager
- IP Professional
- Industry Leading Data Capabilities
- Powerful AI technology
- Patent DNA Extraction
Browse by: Latest US Patents, China's latest patents, Technical Efficacy Thesaurus, Application Domain, Technology Topic, Popular Technical Reports.
© 2024 PatSnap. All rights reserved.Legal|Privacy policy|Modern Slavery Act Transparency Statement|Sitemap|About US| Contact US: help@patsnap.com