Device and method for controlling XY working platform of ultrasonic motor based on neural network
A technology of ultrasonic motor and neural network, applied in electrical program control, piezoelectric effect/electrostrictive or magnetostrictive motor, digital control, etc., can solve the problems of spring static pressure, parameter nonlinear characteristics, influence, etc. , to achieve the effect of large operating frequency range, small DC harmonics, and improved tracking accuracy
- Summary
- Abstract
- Description
- Claims
- Application Information
AI Technical Summary
Problems solved by technology
Method used
Image
Examples
Embodiment Construction
[0059] Embodiments of the present invention will be further described below in conjunction with the accompanying drawings.
[0060] Ultrasonic motor XY work platform control device based on neural network, such as figure 1 As shown, the device includes an ultrasonic motor circuit 1, a resonance tank main circuit, a voltage-controlled oscillator VCO5, a control and drive circuit 4, and a digital signal processor 6, and is characterized in that: the resonance tank main circuit includes current sources connected in parallel Resonance drive circuit, the current source parallel resonance drive circuit includes two current source parallel resonance inverters 2 and 3 with energy feedback function; wherein, the ultrasonic motor circuit 1: is used to control X, Y in the XY work platform Two-axis motion position circuit; resonance tank main circuit: contains two current source parallel resonant inverters with energy feedback function, which controls the positive and negative rotation of...
PUM
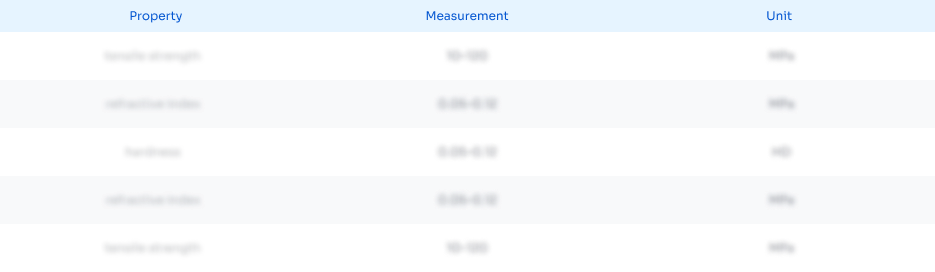
Abstract
Description
Claims
Application Information

- R&D Engineer
- R&D Manager
- IP Professional
- Industry Leading Data Capabilities
- Powerful AI technology
- Patent DNA Extraction
Browse by: Latest US Patents, China's latest patents, Technical Efficacy Thesaurus, Application Domain, Technology Topic, Popular Technical Reports.
© 2024 PatSnap. All rights reserved.Legal|Privacy policy|Modern Slavery Act Transparency Statement|Sitemap|About US| Contact US: help@patsnap.com