Method and device for automatically controlling temperature of optical fiber coatings in wiredrawing process
An automatic control device and a technology of drawing process, applied in the field of optical fiber processing, can solve problems such as difficulty in meeting the requirements of high-speed drawing coating, difficulty in ensuring the quality of optical fiber coating, etc., achieving easy implementation and promotion, simple structure, and avoiding paint overflow. Effect
- Summary
- Abstract
- Description
- Claims
- Application Information
AI Technical Summary
Problems solved by technology
Method used
Image
Examples
Embodiment 1
[0024] Example 1 as figure 1 As shown, it is an electric heating method, including an optical fiber coater 4, and the coating chamber of the optical fiber coater communicates with the material tank through a feed pipe, and the described optical fiber coater is provided with two coating chambers, upper and lower, wherein The upper paint chamber is connected with the upper feed pipe 5, and the upper feed pipe may or may not be provided with a controllable heater, and the lower paint chamber is connected with the lower feed pipe 2, and the outer surface of the lower feed pipe is wound with one layer or more A layer of heating wire constitutes a controllable heater 6, and the temperature of the lower feeding pipeline is measured by a temperature sensor 3. At the same time, the temperature of the heating wire is adjusted by the temperature setting value of the PLC unit connected to it, and the temperature setting value is according to the formula 1 is set, and the wire drawing spee...
Embodiment 2
[0026] Example 2 as figure 2 As shown, the liquid or gas medium heating method differs from the previous embodiment in that the controllable heater 6 is a liquid or gas medium heater, and the liquid or gas medium heater is covered by The annular heating tank of the feed pipeline 2 and the circulation heater 7 connected thereto are formed. The annular heating tank and the circulation heater are filled with liquid or gas medium, and the circulation heater heats the feed pipeline by heating the liquid or gas medium to make the paint Raise the temperature until the coating temperature is close to the temperature of the liquid or gas medium; the temperature sensor of this embodiment is installed in the liquid or gas medium cavity of the circulating heater, and the temperature of the liquid or gas medium is used as the temperature sensing of the feed pipeline to the PLC unit. Other structures are the same as the previous embodiment.
PUM
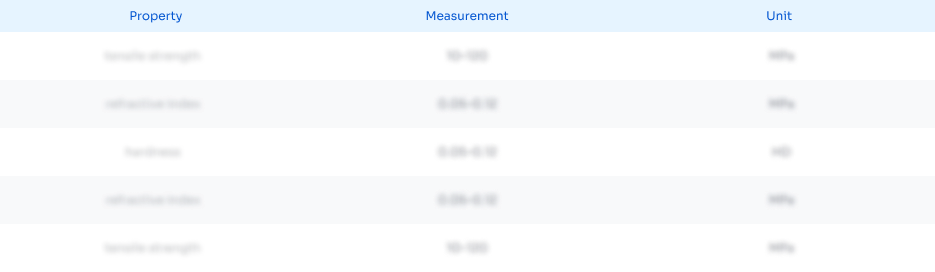
Abstract
Description
Claims
Application Information

- R&D
- Intellectual Property
- Life Sciences
- Materials
- Tech Scout
- Unparalleled Data Quality
- Higher Quality Content
- 60% Fewer Hallucinations
Browse by: Latest US Patents, China's latest patents, Technical Efficacy Thesaurus, Application Domain, Technology Topic, Popular Technical Reports.
© 2025 PatSnap. All rights reserved.Legal|Privacy policy|Modern Slavery Act Transparency Statement|Sitemap|About US| Contact US: help@patsnap.com