Hydraulic jacking system of transporting girder vehicle
A beam transport vehicle and hydraulic technology, which is applied in the direction of parallel load-carrying vehicles, etc., can solve the problems of box girder tilting, poor synchronization performance of hydraulic jacking cylinders, and easy distortion of box girder, so as to achieve the effect of reducing the height of box girder
- Summary
- Abstract
- Description
- Claims
- Application Information
AI Technical Summary
Problems solved by technology
Method used
Image
Examples
Embodiment 1
[0014] Embodiment 1: The jacking system includes a first jacking cylinder 1, a first balance valve 2, a second jacking cylinder 3, a second balance valve 4, a first proportional reversing valve 5, a first ball valve 6, a third Jacking cylinder 7, third balance valve 8, second proportional reversing valve 9, second ball valve 10, third ball valve 11, fourth balancing valve 12, third proportional reversing valve 13, fourth jacking cylinder 14, The fourth ball valve 15 and the fourth proportional reversing valve 16, the rod cavity of the second jacking cylinder 3 and the third jacking cylinder 7 are connected with the second ball valve 10 through a hydraulic pipe, the second jacking cylinder 3 and The rodless cavity of the third jacking cylinder 7 is connected with the first ball valve 6 through a hydraulic pipe; the rod cavity end of the second jacking cylinder 3 is connected with one end of the first proportional reversing valve 5, and the second jacking cylinder The rodless ch...
PUM
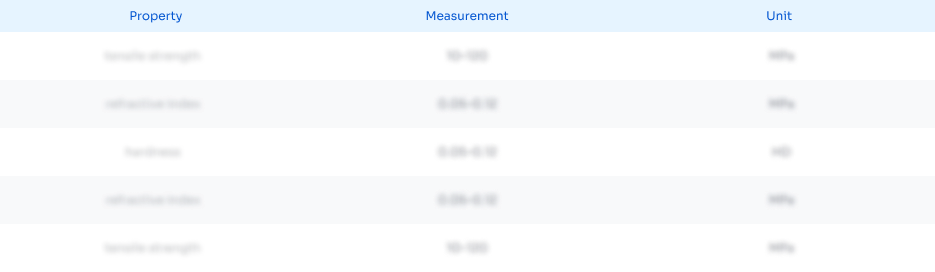
Abstract
Description
Claims
Application Information

- R&D
- Intellectual Property
- Life Sciences
- Materials
- Tech Scout
- Unparalleled Data Quality
- Higher Quality Content
- 60% Fewer Hallucinations
Browse by: Latest US Patents, China's latest patents, Technical Efficacy Thesaurus, Application Domain, Technology Topic, Popular Technical Reports.
© 2025 PatSnap. All rights reserved.Legal|Privacy policy|Modern Slavery Act Transparency Statement|Sitemap|About US| Contact US: help@patsnap.com