Force-control-based magnetic levitation system and control method
A control system and magnetic levitation technology, applied in the field of magnetic levitation, can solve the problems that the bearing capacity of the magnetic bearing cannot reach the high-speed rotor, the displacement of the magnetic bearing cannot be directly measured, and the displacement sensor cannot be directly installed. simplified effect
- Summary
- Abstract
- Description
- Claims
- Application Information
AI Technical Summary
Problems solved by technology
Method used
Image
Examples
Embodiment 1
[0042] Such as figure 2 As shown, a magnetic levitation system based on force control includes a mechanical device and a control system. The mechanical device includes a motor 1, a shaft coupling 2, a force-measuring bearing 3, two radial magnetic bearings 4 and a rotor 5. The control system includes a voltage amplifier, a controller and a power amplifier. The motor 1 is connected to one end of the rotor 5 through a shaft coupling 2, the two ends of the rotor 5 are respectively provided with force-measuring bearings 3, and the two radial magnetic bearings 4 are arranged between the two force-measuring bearings 3 and Corresponding thereto; the input end of the voltage amplifier is connected with the force-measuring bearing, the output end is connected with the input end of the controller, the output end of the controller is connected with the input end of the power amplifier, and the output end of the power amplifier Connect with radial magnetic bearing 4. Wherein, the radial ...
Embodiment 2
[0046] Such as image 3 As shown, a magnetic levitation system based on force control includes a mechanical device and a control system, the mechanical device includes a rotor 5, a quasi-levitation motor 6 and a load bearing 3, and the control system includes a voltage amplifier, a controller and a power amplifier . The two ends of the rotor 5 are respectively provided with a force-measuring bearing 3, and the quasi-levitation motor 6 is arranged between the two force-measuring bearings 3; the input end of the voltage amplifier is connected with the force-measuring bearing, and the output end is connected with the controller The input end of the controller is connected to the input end of the power amplifier, and the output end of the power amplifier is connected to the quasi-levitation motor; wherein, the quasi-levitation motor includes a torque coil sleeved on the rotor windings and quasi-suspension coil windings, the torque coil windings generate electromagnetic torque to ...
Embodiment 3
[0050] Such as Figure 4 As shown, a magnetic levitation system based on force control includes a mechanical device and a control system. The mechanical device includes a motor 1, a coupling 2, a load bearing 3, two radial magnetic bearings 4, a rotor 5 and an axial For a magnetic bearing, the control system includes a voltage amplifier, a controller and a power amplifier. The motor 1 is connected to one end of the rotor 5 through a coupling 2, and the two ends of the rotor 5 are respectively provided with force-measuring bearings 3, and the two radial magnetic bearings 4 are arranged between the two force-measuring bearings and respectively Correspondingly, the axial magnetic bearing is correspondingly arranged between two radial magnetic bearings 4; the input end of the voltage amplifier is connected to the force-measuring bearing, and the output end is connected to the input end of the controller, and the controller The output end of the power amplifier is connected to the...
PUM
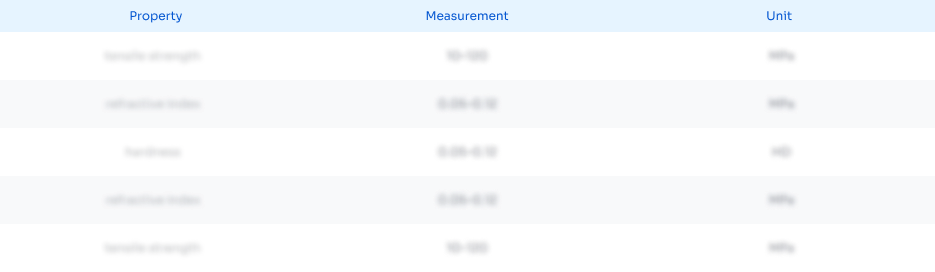
Abstract
Description
Claims
Application Information

- R&D Engineer
- R&D Manager
- IP Professional
- Industry Leading Data Capabilities
- Powerful AI technology
- Patent DNA Extraction
Browse by: Latest US Patents, China's latest patents, Technical Efficacy Thesaurus, Application Domain, Technology Topic, Popular Technical Reports.
© 2024 PatSnap. All rights reserved.Legal|Privacy policy|Modern Slavery Act Transparency Statement|Sitemap|About US| Contact US: help@patsnap.com