Visual system with real-time parameter monitoring and on-line calibration functions
A vision system and calibration technology, applied in the field of vision systems, can solve the problems of large computing workload of vision systems, affecting the accuracy of visual computing, lack of real-time parameter monitoring and online calibration functions, etc., to achieve the effect of ensuring accuracy
- Summary
- Abstract
- Description
- Claims
- Application Information
AI Technical Summary
Problems solved by technology
Method used
Image
Examples
Embodiment approach
[0036] Based on above-mentioned principle, an embodiment of the present invention is as follows:
[0037] see image 3 , which is a schematic diagram of images collected by the vision system in an embodiment of the present invention applied to an unmanned surface vehicle.
[0038] In this example, the image 300 collected by the vision system is divided into a monitoring and marking area 302 and a visual reconstruction area 301 . Wherein the monitoring calibration area 302 shows the image 303 of a calibration object whose relative position is fixed relative to the vision system, which is used for real-time monitoring and online calibration of the parameters of the vision system; The part outside the marked area 302 is the imaging area where the visual system observes the surrounding scene, and is used for visual calculation.
[0039] Since the feature points on the calibration object in the vision system are used for both real-time parameter monitoring and online calibration,...
PUM
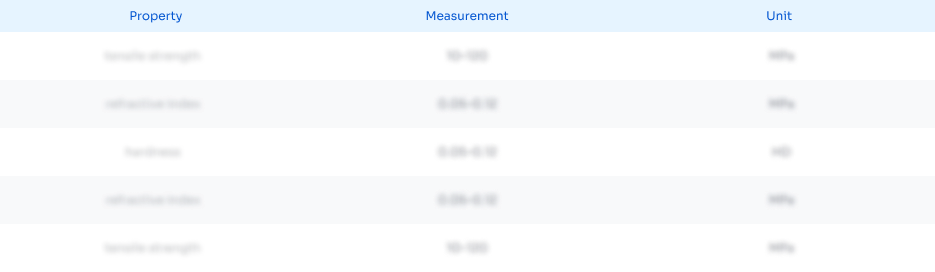
Abstract
Description
Claims
Application Information

- Generate Ideas
- Intellectual Property
- Life Sciences
- Materials
- Tech Scout
- Unparalleled Data Quality
- Higher Quality Content
- 60% Fewer Hallucinations
Browse by: Latest US Patents, China's latest patents, Technical Efficacy Thesaurus, Application Domain, Technology Topic, Popular Technical Reports.
© 2025 PatSnap. All rights reserved.Legal|Privacy policy|Modern Slavery Act Transparency Statement|Sitemap|About US| Contact US: help@patsnap.com