Molded coil and solenoid controlled valve using the same
A solenoid valve and coil technology, applied in coil manufacturing, electromagnets with armatures, coils, etc., can solve problems such as poor electrical contact, inability to fix the socket assembly on the molded coil, and inability to firmly connect the ground terminal 206, etc. , to achieve the effect of reliable electrical contact
- Summary
- Abstract
- Description
- Claims
- Application Information
AI Technical Summary
Problems solved by technology
Method used
Image
Examples
Embodiment Construction
[0072] Hereinafter, embodiments (examples) of the present invention will be described in more detail based on the drawings.
[0073] figure 1 It is a partial cross-sectional view of a solenoid valve in which a valve body is mounted on a valve body mounting hole of a molded coil according to the present invention, figure 2 is in figure 1 A view of the A-A line, image 3 Perspective view of the magnetic frame of the molded coil of the present invention, Figure 4 It is a perspective view showing the state where the ground terminal is connected and fixed to the magnetic frame of the molded coil of the present invention, Figure 5 It is a partially enlarged cross-sectional view illustrating a method for connecting and fixing a ground terminal on a magnetic frame of a molded coil of the present invention, Figure 6 It is a perspective view showing a state where a ground terminal is fixedly connected to a magnetic frame of a molded coil of the present invention and a bobbin i...
PUM
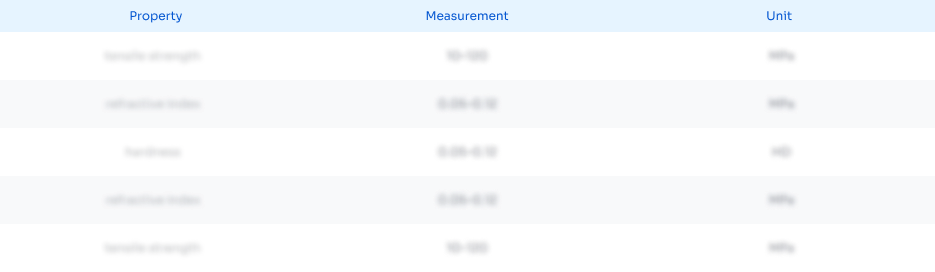
Abstract
Description
Claims
Application Information

- Generate Ideas
- Intellectual Property
- Life Sciences
- Materials
- Tech Scout
- Unparalleled Data Quality
- Higher Quality Content
- 60% Fewer Hallucinations
Browse by: Latest US Patents, China's latest patents, Technical Efficacy Thesaurus, Application Domain, Technology Topic, Popular Technical Reports.
© 2025 PatSnap. All rights reserved.Legal|Privacy policy|Modern Slavery Act Transparency Statement|Sitemap|About US| Contact US: help@patsnap.com