Portable real-time opto-acoustic imaging system
A photoacoustic imaging, portable technology, applied in the direction of material analysis, measuring devices, instruments, etc. through optical means, can solve the problem of system miniaturization and portable structure design, large random errors, affecting imaging quality and time resolution of research results , reliability, stability and other issues, to achieve the effect of good system dynamic response characteristics, compact structure, improved operability and scope of application
- Summary
- Abstract
- Description
- Claims
- Application Information
AI Technical Summary
Problems solved by technology
Method used
Image
Examples
Embodiment 1
[0018] Embodiment 1 The structure of this embodiment is as follows figure 1 As shown, the names of each component are: 1. Central processing unit, 2. Driving circuit, 3. Data acquisition circuit, 4. Signal amplification circuit, 5. Signal preprocessing circuit, 6. Ultrasonic sensor, 7. External interface of the circuit, 8. Laser diode, 9. Collimating lens group, 10. X-axis mirror, 11. Y-axis mirror, 12. Focusing lens group, 13. Protective mirror, 14. X-axis motor, 15. Y-axis motor , 16. Shell.
[0019] Among them, the light source 1 is a pulsed semiconductor laser diode (PGAS1S24, Hoffo), the working wavelength is 905nm, the peak power is 49W, the pulse width is 150ns, and the single pulse energy is about 7.3uJ; the center frequency of the multi-element linear array ultrasonic array sensor 6 is 2.5MHz, the relative bandwidth is 75%, the area is 100mm×10mm×0.8mm, it contains 128 elements, and the slot width between the elements is 0.03mm.
[0020] This embodiment includes a c...
Embodiment 2
[0030] Embodiment 2 A portable real-time photoacoustic imaging system integrating a two-dimensional laser galvanometer and a laser diode. Probe (2.5P9×9K3), the center frequency is 2.5MHz, the size is 9mm×9mm, and the external interface adopts Q9 (BNC) interface.
Embodiment 3
[0031] Embodiment 3 A portable real-time photoacoustic imaging system integrating a two-dimensional laser vibrating mirror and a laser diode. The structure is similar to that of Embodiment 1. Probe (2.5P6×6K2), the center frequency is 2.5MHz, the size is 6mm×6mm, and the external interface adopts Q9 (BNC) interface.
PUM
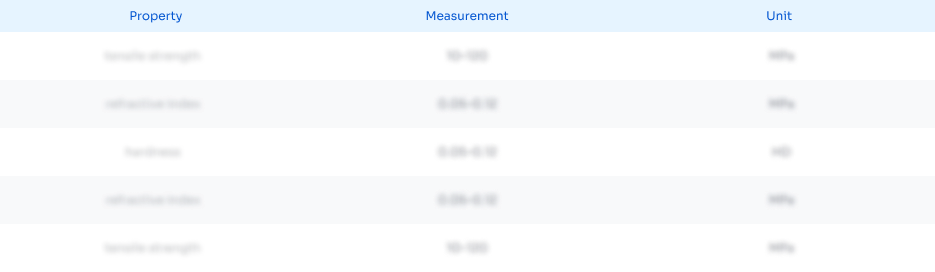
Abstract
Description
Claims
Application Information

- R&D
- Intellectual Property
- Life Sciences
- Materials
- Tech Scout
- Unparalleled Data Quality
- Higher Quality Content
- 60% Fewer Hallucinations
Browse by: Latest US Patents, China's latest patents, Technical Efficacy Thesaurus, Application Domain, Technology Topic, Popular Technical Reports.
© 2025 PatSnap. All rights reserved.Legal|Privacy policy|Modern Slavery Act Transparency Statement|Sitemap|About US| Contact US: help@patsnap.com