Method for assembling heavy core-pulling mechanism of large injection mould
A technology for injection molds and core-pulling mechanisms, applied in the field of assembly of heavy-duty core-pulling mechanisms, can solve the problems of difficult assembly, labor and time-consuming, easy to damage core-pulling sliders, etc., and achieve the effect of solving difficult assembly and avoiding damage
- Summary
- Abstract
- Description
- Claims
- Application Information
AI Technical Summary
Problems solved by technology
Method used
Image
Examples
Embodiment Construction
[0024] refer to Figure 1 to Figure 7 , the assembly method of the heavy-duty core-pulling mechanism of a large-scale injection mold of the present invention is an assembly process method, and the assembly process method is: using a crane,
[0025] Step 1, hoisting the moving model core 1 into the moving model carrier plate 2 in the forward direction;
[0026] Step 2, hoist the movable mold carrier plate 2 and the dynamic model core 1 and turn it to 180°, make the bottom surface of the movable mold carrier plate 2 face up and use the support 01 to level the bottom surface of the movable mold carrier plate 2; the support 01 is a jack;
[0027] Step 3: Use a crane to hang the bottom surface of the core-pulling slider 3 through the lifting ring, lift and slide the profile of the core-pulling slider 3 vertically along the corresponding profile of the movable model core 1, and insert it into the movable mold carrier plate 2 and the movable mold core 1 In the core pulling slot;
...
PUM
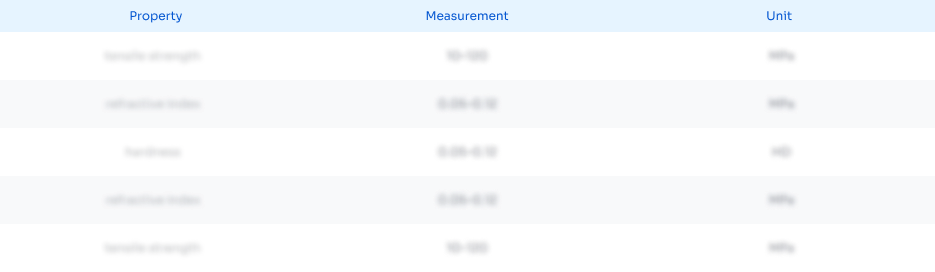
Abstract
Description
Claims
Application Information

- R&D
- Intellectual Property
- Life Sciences
- Materials
- Tech Scout
- Unparalleled Data Quality
- Higher Quality Content
- 60% Fewer Hallucinations
Browse by: Latest US Patents, China's latest patents, Technical Efficacy Thesaurus, Application Domain, Technology Topic, Popular Technical Reports.
© 2025 PatSnap. All rights reserved.Legal|Privacy policy|Modern Slavery Act Transparency Statement|Sitemap|About US| Contact US: help@patsnap.com