Rotor displacement measurement device and method for planar motor
A plane motor, displacement measurement technology, applied in the direction of measuring devices, electrical devices, opto-mechanical equipment, etc., can solve the problems of the grating scale surface being polluted, the use environment is high, and the measurement accuracy is greatly affected by the environment.
- Summary
- Abstract
- Description
- Claims
- Application Information
AI Technical Summary
Problems solved by technology
Method used
Image
Examples
Embodiment
[0070] in m x = m y =4. Take the magnetic field pole distance τ=35.35mm as an example, according to the calculation formula for the maximum number of spatial frequency multiplication operations, select n X =n Y =4, implement the device and method of the present invention.
[0071] The device reference figure 1 The planar motor of the present invention is a moving-coil planar motor including a stator 1 and a mover 3 on the stator 1, the stator 1 includes a magnetic steel array 2, and the lower surface of the mover 3 is provided with a coil array 4; The displacement measuring device includes a probe 5, two groups of sine sensors, two groups of cosine sensors, a signal conducting line 6 and a signal processing circuit 7; Sinusoidal magnetic field area; the two groups of sine sensors include the x-direction sine sensor group 8 and the y-direction sine sensor group 10, and the two groups of cosine sensors include the x-direction cosine sensor group 9 and the y-direction cosine ...
PUM
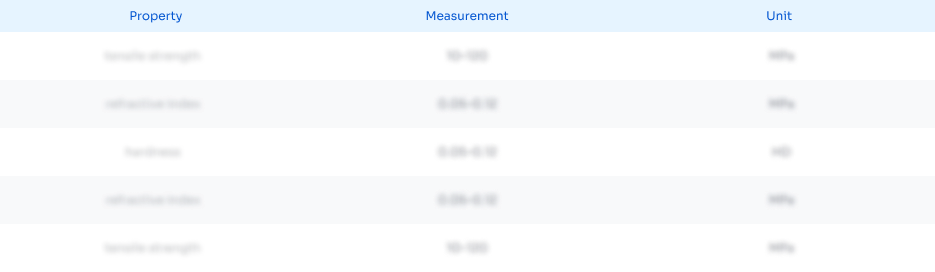
Abstract
Description
Claims
Application Information

- Generate Ideas
- Intellectual Property
- Life Sciences
- Materials
- Tech Scout
- Unparalleled Data Quality
- Higher Quality Content
- 60% Fewer Hallucinations
Browse by: Latest US Patents, China's latest patents, Technical Efficacy Thesaurus, Application Domain, Technology Topic, Popular Technical Reports.
© 2025 PatSnap. All rights reserved.Legal|Privacy policy|Modern Slavery Act Transparency Statement|Sitemap|About US| Contact US: help@patsnap.com