Load-bearing adjustable zero-stiffness electromagnetic vibration isolator and control method thereof
A zero-stiffness, vibration isolator technology, applied in the field of load-bearing adjustable quasi-zero-stiffness electromagnetic vibration isolators and their control, can solve problems such as the lack of vibration isolation effect and the deviation of the vibration isolation system from the quasi-zero stiffness working state.
- Summary
- Abstract
- Description
- Claims
- Application Information
AI Technical Summary
Problems solved by technology
Method used
Image
Examples
Embodiment Construction
[0035] Such as figure 2 As shown, an embodiment of the present invention includes a vibration isolation device 6, a group of electromagnetic springs in the vertical direction, and two groups of electromagnetic springs in the horizontal direction. The outer frame 10 is installed on the left and right sides of the base 11, and the control circuit 9 is also included. The electromagnetic spring includes a set of electromagnets and two permanent magnets. The right side of the vibration isolation device 6 is connected to the first permanent magnet of the right horizontal electromagnetic spring through a connecting rod, and the first permanent magnet of the right horizontal electromagnetic spring is The magnet is connected with the second permanent magnet through the guide bar 4, and the second permanent magnet is connected with the electromagnet, and the electromagnet is fixed on the right outer frame 10; the electromagnetic spring in the vertical direction includes two groups of el...
PUM
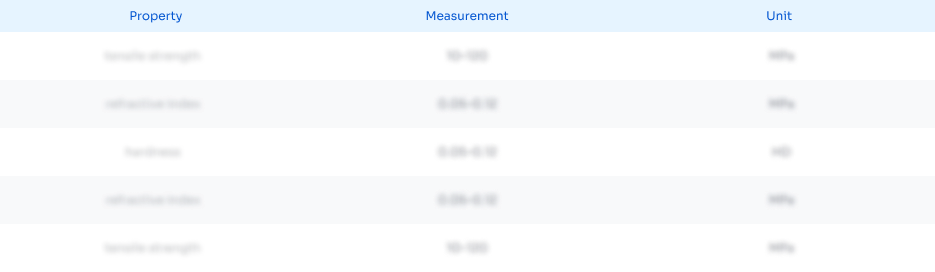
Abstract
Description
Claims
Application Information

- R&D
- Intellectual Property
- Life Sciences
- Materials
- Tech Scout
- Unparalleled Data Quality
- Higher Quality Content
- 60% Fewer Hallucinations
Browse by: Latest US Patents, China's latest patents, Technical Efficacy Thesaurus, Application Domain, Technology Topic, Popular Technical Reports.
© 2025 PatSnap. All rights reserved.Legal|Privacy policy|Modern Slavery Act Transparency Statement|Sitemap|About US| Contact US: help@patsnap.com