Method for determining blanks of different thickness for local loading forming of three-dimensional frame-shaped member
A local loading and billet technology, applied in the field of thick billets, can solve the problems of high cost, failure to consider the local loading characteristics of the mold partition, and the area cannot be filled, etc.
- Summary
- Abstract
- Description
- Claims
- Application Information
AI Technical Summary
Problems solved by technology
Method used
Image
Examples
Embodiment Construction
[0118] This embodiment is a method for determining a three-dimensional frame-shaped component with unequal thickness blanks for local loading and forming. The component in this embodiment is a frame-shaped component 6, such as Figure 4b As shown, the upper surface and the lower surface have ribs distributed symmetrically; the upper mold is divided into two pieces, and the center of the partition rib 8 is the mold partition position; the material of the component is TA15 titanium alloy. The forming process in this embodiment has two loading steps.
[0119] In this embodiment, the isothermal forming process is adopted for the local loading forming of the three-dimensional frame-shaped member, the forming temperature is 970°C, the loading speed of the upper die is 0.2 mm / s, and the friction factor m is taken as 0.3.
[0120] The shape of the component in this embodiment is divided into two sections: one section is located at one end of the component, one side surface of this sec...
PUM
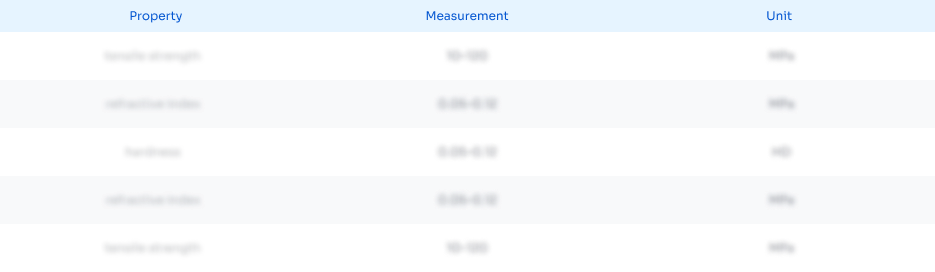
Abstract
Description
Claims
Application Information

- R&D
- Intellectual Property
- Life Sciences
- Materials
- Tech Scout
- Unparalleled Data Quality
- Higher Quality Content
- 60% Fewer Hallucinations
Browse by: Latest US Patents, China's latest patents, Technical Efficacy Thesaurus, Application Domain, Technology Topic, Popular Technical Reports.
© 2025 PatSnap. All rights reserved.Legal|Privacy policy|Modern Slavery Act Transparency Statement|Sitemap|About US| Contact US: help@patsnap.com