Ammonia production process
A technology of ammonia synthesis and ammonia synthesis, which is applied in the field of ammonia preparation, can solve the problems of reducing overall efficiency and accumulation of inert gas, and achieve the effect of increasing load and energy consumption
- Summary
- Abstract
- Description
- Claims
- Application Information
AI Technical Summary
Problems solved by technology
Method used
Image
Examples
no. 1 approach
[0052] According to a first embodiment, the hydrogen separation frame includes TSA molecular sieves or PSA molecular sieves. According to a second embodiment, the hydrogen separation frame comprises a cryogenic separator. A water removal section 152 must be provided with a cryogenic separator.
[0053] The off-gas 19 may be recycled directly as fuel to the primary reformer 101 or used to regenerate the water removal section 152 before being recycled as fuel in said primary reformer 101 .
[0054] For example, the primary reformer 101 is equipped with catalytic tubes. In a preferred embodiment, the operating pressure in the catalytic tubes is greater than 35 bar; preferably 40 to 100 bar, and more preferably 60 to 80 bar.
[0055] The present invention achieves the objects and purposes set forth above. Due to the circulation of hydrogen by means of stream 15, stream 16 and stream 17, the energy consumption of the circulator 140 is slightly increased, which is well compensate...
PUM
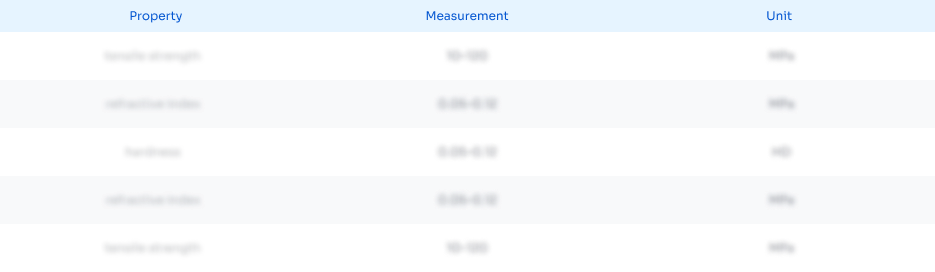
Abstract
Description
Claims
Application Information

- R&D
- Intellectual Property
- Life Sciences
- Materials
- Tech Scout
- Unparalleled Data Quality
- Higher Quality Content
- 60% Fewer Hallucinations
Browse by: Latest US Patents, China's latest patents, Technical Efficacy Thesaurus, Application Domain, Technology Topic, Popular Technical Reports.
© 2025 PatSnap. All rights reserved.Legal|Privacy policy|Modern Slavery Act Transparency Statement|Sitemap|About US| Contact US: help@patsnap.com