Float disc feeding method for planar wafer optical parts
A technology for optical parts and sheets, applied in the field of flat sheet optical parts processing, can solve the problems of uneven pressure, damaged and scrapped parts, material and labor losses, etc., to achieve uniform pressure, reduce deformation, and reduce bonding area. Effect
- Summary
- Abstract
- Description
- Claims
- Application Information
AI Technical Summary
Problems solved by technology
Method used
Image
Examples
Embodiment
[0021] Such as figure 1 , figure 2 As shown, the float method for loading flat sheet optical parts includes the following steps:
[0022] First, cover two layers of lens paper 3 on the bonding surface of the plane thin optical part 4 to be processed, then apply foreign dry varnish, and dry for use;
[0023] Then, evenly smear one layer of castor oil 2 on the bonding mold 1, and the side of the flat sheet optical part covered with lens paper facing the bonding mold is placed on the bonding mold coated with castor oil 2. On the mold 1, and leave a gap between the flat sheet optical parts;
[0024] Finally, hot melt adhesive 5 is filled in the gaps between the planar thin optical parts. The hot melt adhesive may cool during the filling process. At this time, use a soldering iron to melt the hot melt adhesive around the part again to ensure a good bond between the hot melt adhesive and the side of the part. After cooling, the optical parts can be processed.
PUM
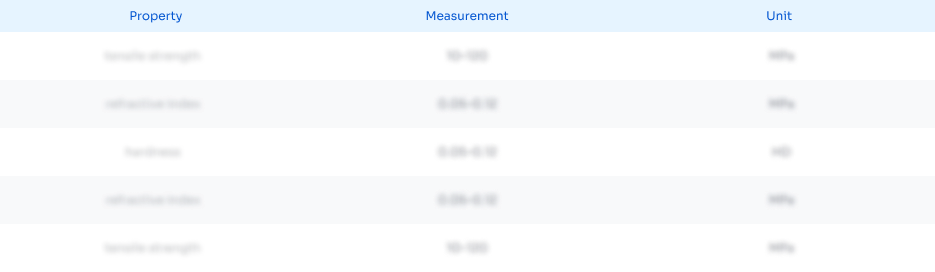
Abstract
Description
Claims
Application Information

- R&D Engineer
- R&D Manager
- IP Professional
- Industry Leading Data Capabilities
- Powerful AI technology
- Patent DNA Extraction
Browse by: Latest US Patents, China's latest patents, Technical Efficacy Thesaurus, Application Domain, Technology Topic, Popular Technical Reports.
© 2024 PatSnap. All rights reserved.Legal|Privacy policy|Modern Slavery Act Transparency Statement|Sitemap|About US| Contact US: help@patsnap.com