Process method for forging low door type front axle of heavy commercial vehicle
A process method and technology for commercial vehicles, which are applied in vehicle parts, railway car body parts, transportation and packaging, etc., can solve the problems of decreased die life, affected equipment load, and many quality problems, and improved the average qualification rate of forging. The effect of forging qualification rate and improving production efficiency
- Summary
- Abstract
- Description
- Claims
- Application Information
AI Technical Summary
Problems solved by technology
Method used
Examples
Embodiment Construction
[0018] The forging process method of the front axle of a low-door heavy commercial vehicle described in the embodiment of the present invention, the main process includes:
[0019] 1. Calculation of forging force
[0020] In the calculation process of forging force, according to our previous experience formula:
[0021] F=P*A formula
[0022] (P is the empirical coefficient, A is the projected area of the forging)
[0023] The empirical coefficient P is selected according to the routine 7, and the projected area A is 222519.8mm 2 After calculation, the forging forming force has reached 155.7MN, exceeding the maximum forging force of our company of 125MN. If we consider the heating temperature difference of the blank and the unevenness of the blank, and the requirements for the forging to be fully filled, the tooling and mold are carried out according to the routine. It will cause the equipment to be overloaded and unable to produce, and it will be impossible to develop. ...
PUM
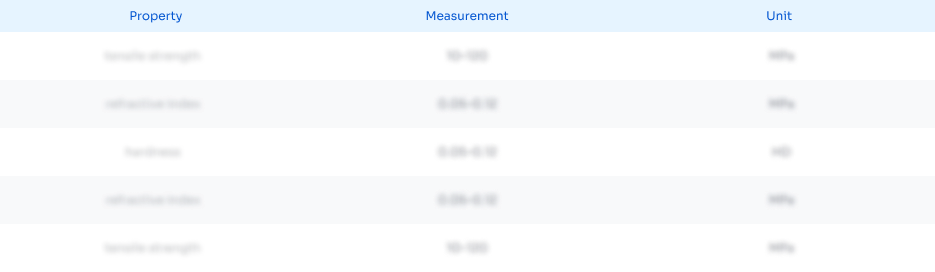
Abstract
Description
Claims
Application Information

- R&D Engineer
- R&D Manager
- IP Professional
- Industry Leading Data Capabilities
- Powerful AI technology
- Patent DNA Extraction
Browse by: Latest US Patents, China's latest patents, Technical Efficacy Thesaurus, Application Domain, Technology Topic, Popular Technical Reports.
© 2024 PatSnap. All rights reserved.Legal|Privacy policy|Modern Slavery Act Transparency Statement|Sitemap|About US| Contact US: help@patsnap.com