Front axle carrier with integrated steering box
一种前桥托架、转向箱的技术,应用在下部结构、运输和包装、车辆部件等方向,能够解决高材料成本和制造成本等问题,达到高弯曲强度、结构组件简化、节省制造成本的效果
- Summary
- Abstract
- Description
- Claims
- Application Information
AI Technical Summary
Problems solved by technology
Method used
Image
Examples
Embodiment Construction
[0029] figure 1A first exemplary embodiment of the inventive front axle carrier with integrated steering box is shown by way of example. The front axle bracket consists of longitudinal brackets 1, 2, fastening elements 3, 4 for the positioning of the wheel guide elements. The longitudinal brackets 1, 2 are connected to the steering box 5 by welding, and the steering box simultaneously functions as a transverse bracket. The longitudinal brackets 1, 2 are formed in the rear section from sheet steel shells 1.1, 1.2, 2.1, 2.2 welded together. These sheet steel shells have openings 7 , 8 for bolting or screwing the front axle carrier to the motor vehicle body. The rear and central openings 7 , 8 have notches on their retaining faces, which limit damage to the connecting parts in the event of a crash. The sheet steel profiles 1.2, 2.2 with centrally located openings 8 or fastenings are mounted on the longitudinal brackets 1, 2 and welded to them. Furthermore, supports or fixings...
PUM
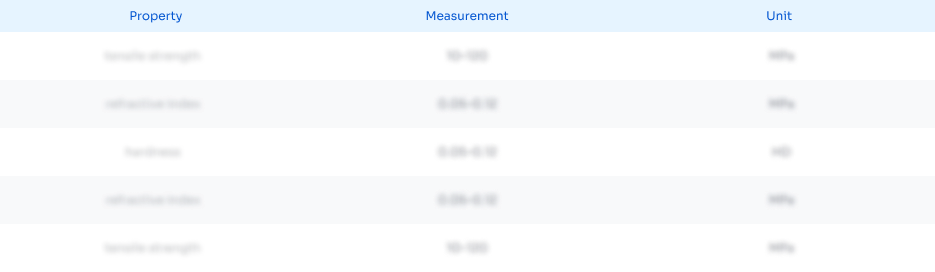
Abstract
Description
Claims
Application Information

- Generate Ideas
- Intellectual Property
- Life Sciences
- Materials
- Tech Scout
- Unparalleled Data Quality
- Higher Quality Content
- 60% Fewer Hallucinations
Browse by: Latest US Patents, China's latest patents, Technical Efficacy Thesaurus, Application Domain, Technology Topic, Popular Technical Reports.
© 2025 PatSnap. All rights reserved.Legal|Privacy policy|Modern Slavery Act Transparency Statement|Sitemap|About US| Contact US: help@patsnap.com