Straight-pull cold-rolling mill tension control method based on speed feedforward
A technology of tension control and feedforward control, applied in the direction of tension/pressure control, etc., can solve the problems that cannot be satisfied at the same time
- Summary
- Abstract
- Description
- Claims
- Application Information
AI Technical Summary
Problems solved by technology
Method used
Image
Examples
Embodiment 1
[0145] A 450mm straight-pull reversible cold-rolling experimental rolling mill in a technical center is adopted. The relevant parameters of the system are as follows:
[0146] Tension hydraulic cylinder inner diameter: 125mm, rod diameter: 90mm, maximum stroke: 2100mm, maximum tension: 100kN, maximum speed: 0.4m / s, tension hydraulic cylinder built-in displacement sensor model: RHM2150MD701S1G2100, high pressure oil source pressure: 23.5MPa, high pressure Model of oil pressure sensor: HDA3844-A-250-000; MOOG servo valve is used for flow control, model: D661-4444C G60JOAA6VSX2HA. The tension control system adopts Siemens S7400PLC, the CPU unit used is CPU416-2DP+FM458-1DP, and the tension controller runs in FM458-1DP.
[0147] Raw material specifications: thickness 3.05mm, width 310mm, length 600mm, variety SPCC,
[0148] Target thickness: 0.5mm,
[0149] Rolling passes: 7,
[0150] Maximum rolling speed: 0.25m / s.
[0151] Taking the seventh rolling pass as an example, the e...
PUM
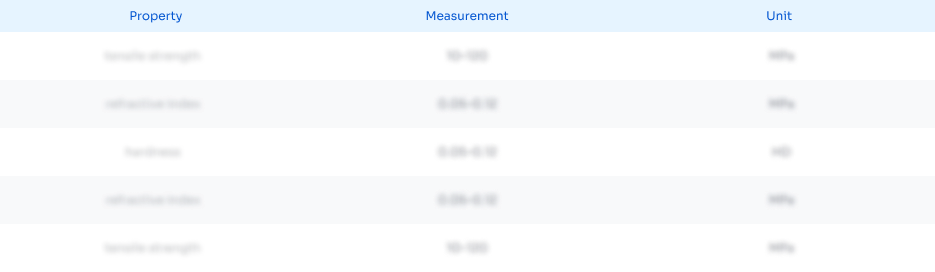
Abstract
Description
Claims
Application Information

- R&D
- Intellectual Property
- Life Sciences
- Materials
- Tech Scout
- Unparalleled Data Quality
- Higher Quality Content
- 60% Fewer Hallucinations
Browse by: Latest US Patents, China's latest patents, Technical Efficacy Thesaurus, Application Domain, Technology Topic, Popular Technical Reports.
© 2025 PatSnap. All rights reserved.Legal|Privacy policy|Modern Slavery Act Transparency Statement|Sitemap|About US| Contact US: help@patsnap.com