Composite swirl combustion chamber
A technology of combustion chambers and composite rolls, applied in combustion engines, internal combustion piston engines, machines/engines, etc., can solve problems such as low air utilization, poor oil-gas mixing, and reduced fuel injection penetration, and achieve fuel distribution expansion, The effect of high air utilization rate, mixing and accelerated combustion
- Summary
- Abstract
- Description
- Claims
- Application Information
AI Technical Summary
Problems solved by technology
Method used
Image
Examples
specific Embodiment
[0038] The CFD three-dimensional mesh models of the composite plume combustor, ω combustor, double plume combustor and side plume combustor under the same compression ratio were respectively established for simulation calculation comparison. Among them, the structures of the basic double-plume combustor, ω combustor, double-plump combustor and side swirl combustor are determined by parametric design.
[0039] The design parameters and calculation settings of the combustion chamber are: eight-hole fuel injector is suitable, the cylinder diameter is 132mm, the stroke is 145mm, the connecting rod length is 262mm, and the clearance height is 2.5mm.
[0040] Calculated according to the compression ratio of 13.5, the volume of the compound plume combustion chamber should be 107510mm 3 . The actual modeling volume is 106506mm 3 , with a deviation rate of 0.93%. In terms of geometric dimensions, the center cone angle is 119°, the cone point height is 5.4mm, the depth of the outer c...
PUM
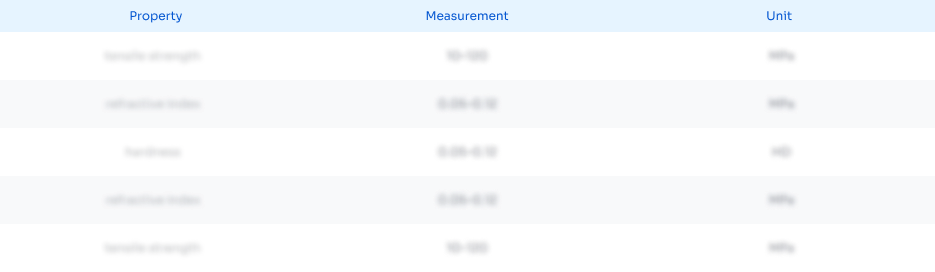
Abstract
Description
Claims
Application Information

- R&D
- Intellectual Property
- Life Sciences
- Materials
- Tech Scout
- Unparalleled Data Quality
- Higher Quality Content
- 60% Fewer Hallucinations
Browse by: Latest US Patents, China's latest patents, Technical Efficacy Thesaurus, Application Domain, Technology Topic, Popular Technical Reports.
© 2025 PatSnap. All rights reserved.Legal|Privacy policy|Modern Slavery Act Transparency Statement|Sitemap|About US| Contact US: help@patsnap.com