Cold-pressing one-step forming method for disc brake pad
A disc brake pad and forming method technology, which is applied in the field of automobile brake systems, can solve problems such as high investment in personnel equipment and electricity costs, uneven distribution of materials, and poor product quality, so as to save hot pressing processes and stabilize product quality , the effect of loose surface
- Summary
- Abstract
- Description
- Claims
- Application Information
AI Technical Summary
Problems solved by technology
Method used
Examples
preparation example Construction
[0032] The preparation method of the cold-pressed resin adhesive is as follows: first put the weighed phenol and formaldehyde into the reaction kettle, start stirring and heat up, first raise the temperature to 75-85°C and keep it warm for 110-130 minutes, and then continue to heat up And assist vacuum dehydration until the temperature is 95~105°C and the vacuum degree is -0.012~-0.008MPa, stop vacuuming and lower the temperature, and add hexamethylenetetramine and hardness regulator when the temperature reaches 78~82°C. Stir well, filter and pack.
[0033] Step 3, Cold Press Forming
[0034] First put the steel back coated in step 2 into the bottom of the cavity of the mold, with the glued side of the steel back facing up, and then fill the steel back with the brake pad reinforcement material made by dry mixing in step 1 In the upper cavity, cold pressing is performed, and the cold pressing time is 10 to 20 seconds. When cold pressing, a press of more than 200 tons is select...
Embodiment 1
[0040] Disc brake pads are manufactured according to the implementation steps in the specific embodiment. Among them, the mass parts of each component of the brake pad reinforcement material are as follows: 15 parts of molybdenum modified phenolic resin, 5 parts of hardness modifier, 20 parts of silica fume cotton, 25 parts of precipitated barium sulfate, 10 parts of steel fiber, aluminum silicate hollow ball 8 parts, expanded vermiculite 15 parts, artificial graphite 10 parts, stone tar 10 parts, TY002 (polyimide resin) 2 parts.
Embodiment 2
[0042] Disc brake pads are manufactured according to the implementation steps in the specific embodiment. Among them, the mass parts of each component of the brake pad reinforcement material are as follows: 18 parts of molybdenum modified phenolic resin, 1 part of hardness modifier, 20 parts of silica fume cotton, 20 parts of precipitated barium sulfate, 5 parts of steel fiber, aluminum silicate hollow ball 10 parts, 12 parts of expanded vermiculite, 8 parts of artificial graphite, 5 parts of stone tar, 2 parts of TY002 (polyimide resin).
PUM
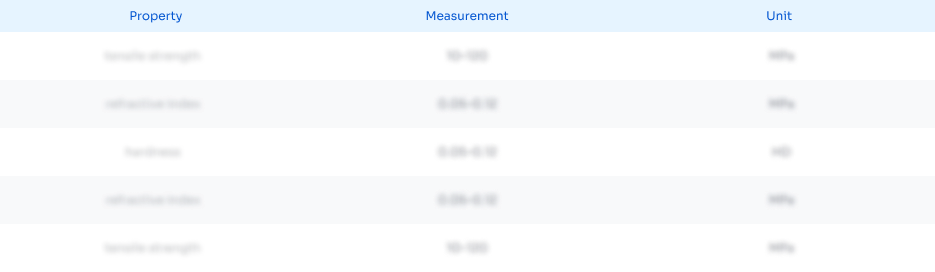
Abstract
Description
Claims
Application Information

- R&D
- Intellectual Property
- Life Sciences
- Materials
- Tech Scout
- Unparalleled Data Quality
- Higher Quality Content
- 60% Fewer Hallucinations
Browse by: Latest US Patents, China's latest patents, Technical Efficacy Thesaurus, Application Domain, Technology Topic, Popular Technical Reports.
© 2025 PatSnap. All rights reserved.Legal|Privacy policy|Modern Slavery Act Transparency Statement|Sitemap|About US| Contact US: help@patsnap.com