Y-shaped cavity orthogonal polarization laser-based force and mass measurement method and device
A technology of orthogonal polarization and quality measurement, applied in the field of laser measurement, which can solve the problems of nonlinearity, low precision, and poor anti-interference ability.
- Summary
- Abstract
- Description
- Claims
- Application Information
AI Technical Summary
Problems solved by technology
Method used
Image
Examples
Embodiment Construction
[0062] exist figure 1 Among them, the force and mass measurement device based on the Y-cavity orthogonally polarized laser includes a Y-cavity orthogonally polarized laser 100, a gas bellows 200, a force unit 300, a working point selection and control unit 400, and a signal acquisition and processing unit 500 .
[0063] The force applying unit 300 adopts a common lever or other force transmission methods.
[0064] The working point selection and control unit 400 includes a first photodetector 401 , a second photodetector 402 , and a working point selection and control circuit 403 . The first photodetector 401 receives the S-polarized light emitted by the S subsection from the Y-cavity orthogonally polarized laser 100 and converts it into a voltage signal, and the second photodetector 401 receives the P polarized light from the Y-cavity orthogonally polarized laser 100 The P-polarized light emitted by the sub-section is converted into a voltage signal. The operating point se...
PUM
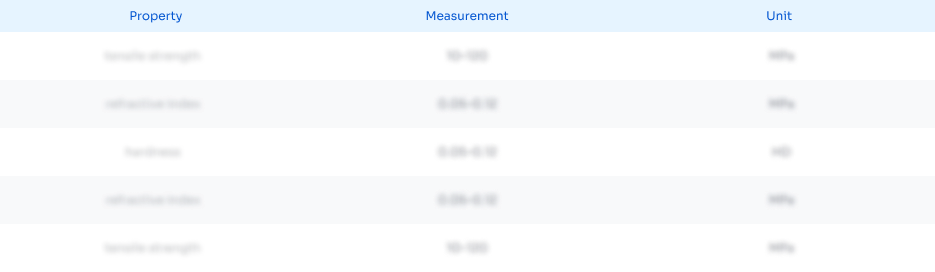
Abstract
Description
Claims
Application Information

- Generate Ideas
- Intellectual Property
- Life Sciences
- Materials
- Tech Scout
- Unparalleled Data Quality
- Higher Quality Content
- 60% Fewer Hallucinations
Browse by: Latest US Patents, China's latest patents, Technical Efficacy Thesaurus, Application Domain, Technology Topic, Popular Technical Reports.
© 2025 PatSnap. All rights reserved.Legal|Privacy policy|Modern Slavery Act Transparency Statement|Sitemap|About US| Contact US: help@patsnap.com