Modified rubber prepared by oil shale waste slag and method for preparing modified rubber by oil shale waste slag
A technology for oil shale ash and modified rubber, applied in the field of ash modified rubber, can solve the problems of increased carbon dioxide emissions, low added value of building materials, waste of resources, etc., and achieves reduction of carbon dioxide emissions, low cost, and energy saving Effect
- Summary
- Abstract
- Description
- Claims
- Application Information
AI Technical Summary
Problems solved by technology
Method used
Examples
Embodiment 1
[0043] a. Crushing the oil shale ash after oil extraction to <300 mesh;
[0044] b. Put it into a high-temperature furnace with a roasting temperature of 500-700°C, keep it warm for 1-2 hours without air, and cool down with the furnace to make carbonized oil shale ash;
[0045] c. Mix 20-40 parts of carbonized oil shale ash, 100 parts of nitrile rubber, styrene-butadiene rubber or butadiene rubber, 60-80 parts of carbon black, 4 parts of stearic acid, 5 parts of zinc oxide, and 1.5 parts of sulfur powder Put 1.5 parts of any one of vulcanization accelerator M, vulcanization accelerator D, vulcanization accelerator TT, vulcanization accelerator H, vulcanization accelerator ZDMC, vulcanization accelerator ZBX or vulcanization accelerator NA-22 into the mixer;
[0046] d. Mixing at 110-130°C for 13-20 minutes;
[0047] e. Molding in a flat vulcanizer after cooling.
[0048] The mechanical properties of the test samples all meet the GB3778-94 standard.
Embodiment 2
[0050] a. Crushing the oil shale ash after oil extraction to <300 mesh;
[0051] b. Put it into a high-temperature furnace with a roasting temperature of 500-700°C, keep it warm for 1-2 hours without air, and cool down with the furnace to make carbonized oil shale ash;
[0052] c. Mix 20-40 parts of carbonized oil shale ash, 100 parts of nitrile rubber, styrene-butadiene rubber or butadiene rubber, 60-80 parts of carbon black, 4 parts of stearic acid, 5 parts of zinc oxide, and 1.5 parts of sulfur powder Put 1.5 parts of any one of vulcanization accelerator M, vulcanization accelerator D, vulcanization accelerator TT, vulcanization accelerator H, vulcanization accelerator ZDMC, vulcanization accelerator ZBX or vulcanization accelerator NA-22 into the mixer;
[0053] d. Mixing at 110-130°C for 13-20 minutes;
[0054] e. Molding in a flat vulcanizer after cooling.
[0055] The mechanical properties of the test samples all meet the GB3778-94 standard.
Embodiment 3
[0057] a. Crushing the oil shale ash after oil extraction to <300 mesh;
[0058] b. Put it into a high-temperature furnace with a roasting temperature of 500-700°C, keep it warm for 1-2 hours without air, and cool down with the furnace to make carbonized oil shale ash;
[0059]c. Mix 20-40 parts of carbonized oil shale ash, 100 parts of nitrile rubber, styrene-butadiene rubber or butadiene rubber, 60-80 parts of carbon black, 4 parts of stearic acid, 5 parts of zinc oxide, and 1.5 parts of sulfur powder Put 1.5 parts of any one of vulcanization accelerator M, vulcanization accelerator D, vulcanization accelerator TT, vulcanization accelerator H, vulcanization accelerator ZDMC, vulcanization accelerator ZBX or vulcanization accelerator NA-22 into the mixer;
[0060] d. Mixing at 110-130°C for 13-20 minutes;
[0061] e. Molding in a flat vulcanizer after cooling.
[0062] The mechanical properties of the test samples all meet the GB3778-94 standard.
PUM
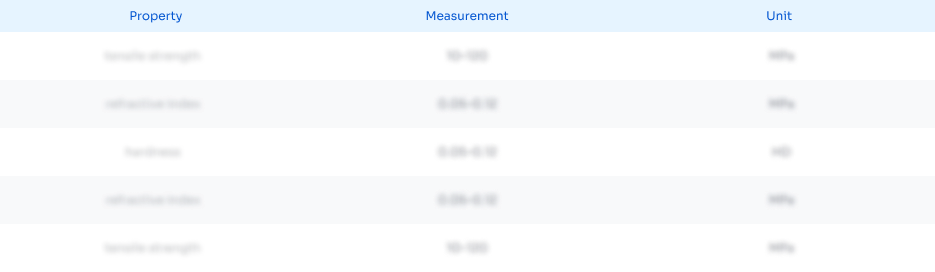
Abstract
Description
Claims
Application Information

- R&D Engineer
- R&D Manager
- IP Professional
- Industry Leading Data Capabilities
- Powerful AI technology
- Patent DNA Extraction
Browse by: Latest US Patents, China's latest patents, Technical Efficacy Thesaurus, Application Domain, Technology Topic, Popular Technical Reports.
© 2024 PatSnap. All rights reserved.Legal|Privacy policy|Modern Slavery Act Transparency Statement|Sitemap|About US| Contact US: help@patsnap.com