Injection-compression molding method for glass fiber reinforced plastic fairing of locomotive
A technology of injection molding and glass fiber reinforced plastic, applied in the direction of coating, can solve the problems of inability to guarantee the size and finish of the back, high material requirements, poor effect, etc., to achieve economical and environmentally friendly appearance, reduce resin content, and ensure strength. Effect
- Summary
- Abstract
- Description
- Claims
- Application Information
AI Technical Summary
Problems solved by technology
Method used
Image
Examples
Embodiment Construction
[0023] The injection molding method of the locomotive FRP fairing of the present invention is made according to the following steps:
[0024] The first step is to make the upper mold; use the existing mold as the lower mold 2, leave a gap according to the thickness and shape of the product, and paste a set of upper mold 1, the upper mold 1 is fixed in the upper mold frame 3, and the lower mold 2 is fixed In the lower mold frame 7, the upper mold 1 is located directly above the lower mold 2, and the position where the upper mold 1 contacts the lower mold 2 is provided with a sealing strip, and a cavity 8 with the same shape as the product is formed between the upper mold 1 and the lower mold 2 , the top of the upper mold 1 has a glue injection port 4, and a plurality of air extraction holes 5 are opened around the glue injection port 4, and the upper mold frame 3 and the lower mold frame 7 are closed with the mold clamping guide mechanism 6;
[0025] The second step is layering...
PUM
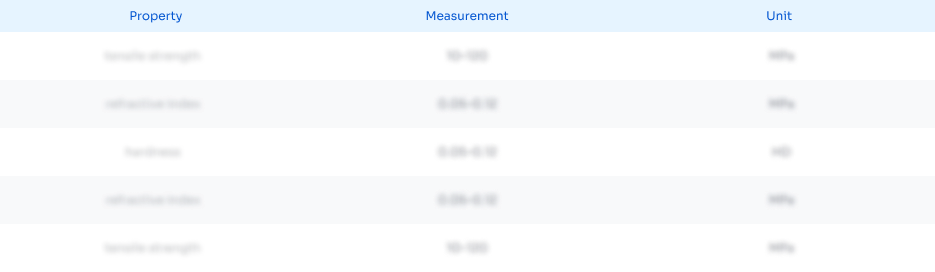
Abstract
Description
Claims
Application Information

- R&D Engineer
- R&D Manager
- IP Professional
- Industry Leading Data Capabilities
- Powerful AI technology
- Patent DNA Extraction
Browse by: Latest US Patents, China's latest patents, Technical Efficacy Thesaurus, Application Domain, Technology Topic, Popular Technical Reports.
© 2024 PatSnap. All rights reserved.Legal|Privacy policy|Modern Slavery Act Transparency Statement|Sitemap|About US| Contact US: help@patsnap.com