Energy-saving implementation method applied to preparing composite materials by means of vertical drying and curing
A curing method and composite material technology, applied in the field of energy-saving structure, can solve the problems of uneconomical and environmental protection, high equipment cost and high use cost
- Summary
- Abstract
- Description
- Claims
- Application Information
AI Technical Summary
Problems solved by technology
Method used
Image
Examples
Embodiment Construction
[0063] In order to make the technical means, creative features, goals and effects achieved by the present invention easy to understand, the present invention will be further described below in conjunction with specific illustrations.
[0064] The following are three specific embodiments of the present invention.
[0065] Option One:
[0066] Such as figure 2 As shown, the fresh air is pressed into the heat exchanger (212a, 212a, 208c) inside the second volatilization section 230 by the air inlet (211a, 211d) of the solidification section 240 via the air intake fan (208a, 208c) controlled by the temperature sensor 213b and the temperature controller 214b. 212b), enter the solidification section 240 after heat exchange with the second volatilization section 230 , and become the source of fresh air for the solidification section 240 . The upper part of the curing section 240 is provided with an air curtain fan 209 a and a top sealing device 210 , preventing the gas in the curi...
PUM
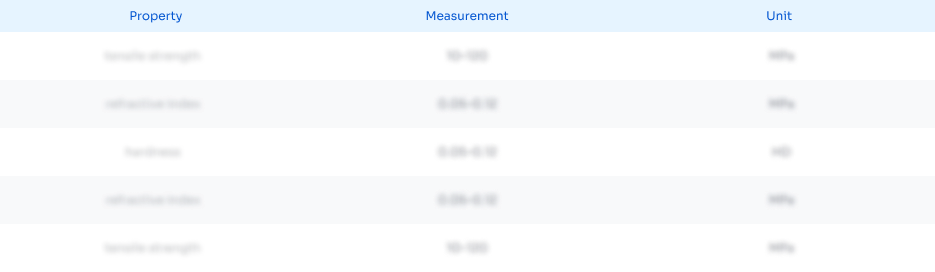
Abstract
Description
Claims
Application Information

- R&D Engineer
- R&D Manager
- IP Professional
- Industry Leading Data Capabilities
- Powerful AI technology
- Patent DNA Extraction
Browse by: Latest US Patents, China's latest patents, Technical Efficacy Thesaurus, Application Domain, Technology Topic, Popular Technical Reports.
© 2024 PatSnap. All rights reserved.Legal|Privacy policy|Modern Slavery Act Transparency Statement|Sitemap|About US| Contact US: help@patsnap.com