Planar articulated robot arm mechanism
A robot arm, plane multi-joint technology, applied in manipulators, claw arms, manufacturing tools, etc., can solve problems such as stiffness reduction, improve reliability, meet the effect of simple structure, flexible and reliable movement
- Summary
- Abstract
- Description
- Claims
- Application Information
AI Technical Summary
Problems solved by technology
Method used
Image
Examples
Embodiment 1
[0023] Example 1: Such as Figure 1-Figure 4 As shown, this example includes a drive unit 1, a base platform 2 and a double telescopic arm assembly 13. The drive unit 1 has two rotating shafts that are nested with each other-a rotating shaft inner shaft 27 and a rotating shaft outer shaft 26. The base platform 2 of the rotating shaft is connected to the lifting mechanism of the drive unit 1, and the dual telescopic arm assembly 13 is symmetrically installed on the base platform 2 with respect to the rotation axis x of the drive unit 1 through the fourth and fifth rotating joints x4, x5 On the outer shaft 26 of the rotary shaft, the inner shaft 27 of the rotary shaft is fixed to the common driving link 3 of the double telescopic arm assembly 13, and the lifting shaft 24, the outer shaft 26 of the rotary shaft and the inner shaft 27 of the rotary shaft respectively pass The independent motors are connected to the controller of the drive unit 1.
[0024] Such as figure 2 , image 3...
Embodiment 2
[0033] Example 2: Such as Figure 5 As shown, the overall structure of this example is the same as that of Embodiment 1, except that the third motor 16 of the inner shaft 27 of the rotating shaft in this example is mounted on the outer shaft 26 of the rotating shaft, and the two pulleys of the synchronous belt transmission mechanism They are respectively connected to the outer shaft 26 of the rotating shaft and the third motor 16. In this way, the outer shaft 26 of the rotating shaft and the inner shaft 27 of the rotating shaft are no longer independently driven. When the inner shaft 27 of the rotating shaft remains stationary and the outer shaft 26 of the rotating shaft rotates, the dual SCARA arm assembly makes an overall rotary movement; regardless of the outer shaft 26 of the rotating shaft For any movement, when the inner shaft 27 of the rotating shaft moves, the double SCARA arm components all make a telescopic movement.
Embodiment 3
[0034] Example 3: Such as Image 6 As shown, the difference between this embodiment and Embodiment 1 is: the drive unit 1 of this example has a rotating shaft—the inner shaft 27 of the rotating shaft. The base platform 2 with the built-in inner shaft 27 of the rotating shaft is connected to the lifting mechanism of the drive unit 1. Above, the double telescopic arm assembly 13 is installed on the base platform 2 symmetrically with respect to the rotation axis x of the drive unit 1 through the fourth and fifth rotary joints X4 and X5, namely: the first and second telescopic arm assemblies 13 The first pulley 17 in the boom 5, 9 is fixed on the base platform 2, and the inner shaft 27 of the rotating shaft is hinged with the first and second booms 5, 9 of the double telescopic arm assembly 13 through the common drive link 3 The lifting shaft 24 and the inner shaft 27 of the rotating shaft of the lifting mechanism are connected to the controller 28 of the driving unit 1 through the ...
PUM
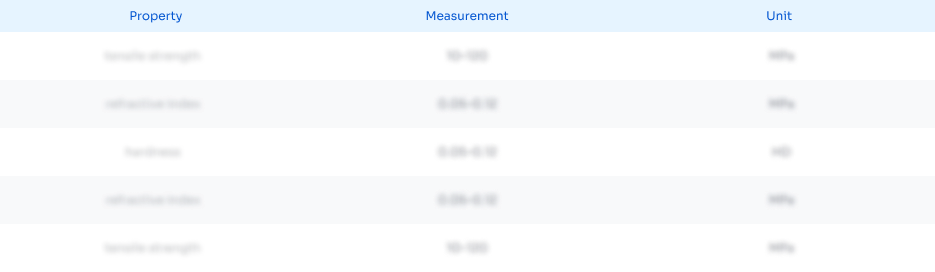
Abstract
Description
Claims
Application Information

- R&D
- Intellectual Property
- Life Sciences
- Materials
- Tech Scout
- Unparalleled Data Quality
- Higher Quality Content
- 60% Fewer Hallucinations
Browse by: Latest US Patents, China's latest patents, Technical Efficacy Thesaurus, Application Domain, Technology Topic, Popular Technical Reports.
© 2025 PatSnap. All rights reserved.Legal|Privacy policy|Modern Slavery Act Transparency Statement|Sitemap|About US| Contact US: help@patsnap.com