Servo controller
A technology of servo controllers and controllers, applied in the field of servo controllers, can solve problems such as small changes, large changes, and fluctuations
- Summary
- Abstract
- Description
- Claims
- Application Information
AI Technical Summary
Problems solved by technology
Method used
Image
Examples
Embodiment approach 1
[0025] figure 1 It is a block diagram showing the configuration of the servo controller according to Embodiment 1 of the present invention. figure 2 yes means figure 1 A block diagram of a configuration example of the instruction generator shown.
[0026] exist figure 1 Among them, the servo controller 1 a drives the motor 4 incorporated in the load device 3 according to the position command A input from the controller 2 . A low-resolution position detector (ENC) 5 is mounted directly on or near the motor 4 . The servo controller 1 a uses the motor position information 251 detected by the position detector 5 as a feedback signal when driving the motor 4 .
[0027] The servo controller 1 a has: a command generator 10 ; a feedforward controller 11 a ; and a feedback controller 12 .
[0028] The instruction generator 10 will be described in detail later, and it uses, for example, figure 2 In the structure shown, the position command A input from the controller 2 is conver...
Embodiment approach 2
[0049] Figure 5 It is a block diagram showing the configuration of the servo controller according to Embodiment 2 of the present invention. In addition, in Figure 5 in, for with figure 1 The same or equivalent components shown in (Embodiment 1) are denoted by the same reference numerals. Here, description will be made centering on parts related to Embodiment 2. FIG.
[0050] Such as Figure 5 As shown, the servo controller 1b according to the second embodiment is configured such that figure 1 In the servo controller 1a shown in (Embodiment 1), a feedforward controller 11b is provided instead of the feedforward controller 11a.
[0051] The feed-forward controller 11b is called a so-called model-following type, which simulates the ideal motion of motors and machines including motors, and performs control in a manner to follow the ideal motion. The feed-forward controller 11b has an adder 120, a model position control 121, adder 122, model speed controller 123, motor mode...
PUM
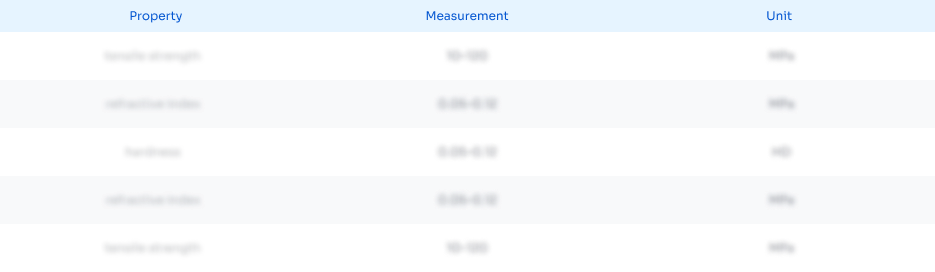
Abstract
Description
Claims
Application Information

- R&D
- Intellectual Property
- Life Sciences
- Materials
- Tech Scout
- Unparalleled Data Quality
- Higher Quality Content
- 60% Fewer Hallucinations
Browse by: Latest US Patents, China's latest patents, Technical Efficacy Thesaurus, Application Domain, Technology Topic, Popular Technical Reports.
© 2025 PatSnap. All rights reserved.Legal|Privacy policy|Modern Slavery Act Transparency Statement|Sitemap|About US| Contact US: help@patsnap.com