Method for treating tail gas generated by sulfur dioxide production
A sulfur dioxide and treatment method technology, which is applied in the direction of chemical instruments and methods, separation methods, dispersed particle separation, etc., can solve the problems of high cost and large pollution, achieve the effect of great significance, low investment cost, and ensure the drying effect
- Summary
- Abstract
- Description
- Claims
- Application Information
AI Technical Summary
Problems solved by technology
Method used
Image
Examples
Embodiment 1
[0022] The sulfur dioxide tail gas treated by the absorption tower is introduced into the gas-liquid separator, and the sulfur dioxide tail gas volume is 5500Nm 3 / h, the sulfur dioxide content is 700mg / Nm 3 , pressure 1kp, gas temperature 40°C. The water content of sulfur dioxide tail gas before separation is 15g / Nm 3 , the water content after separation is 2g / Nm 3 .
[0023] The sulfur dioxide tail gas drawn from the gas-liquid separator enters the drying tower for drying. The drying is filled with structured packing, and the acid divider is sprayed, with a spray volume of 30M 3 / h, drying acid temperature 40 ℃.
[0024] The dried sulfur dioxide tail gas is led to the mixer, and mixed with the pure oxygen from the oxygen system to form a mixed gas, so that the oxygen content increases from 10% to 20% (supplementing oxygen makes the oxygen content of the tail gas reach the normal oxygen content standard of air);
[0025] The mixed gas is sent to the fan, which is then...
Embodiment 2
[0027] The sulfur dioxide tail gas treated by the absorption tower is introduced into the gas-liquid separator, and the sulfur dioxide tail gas volume is 3000Nm 3 / h, the sulfur dioxide content is 346mg / Nm 3 , pressure 0.6kp, gas temperature 40°C. The water content of sulfur dioxide tail gas before separation is 13g / Nm 3 , the water content after separation is 2g / Nm 3 .
[0028] The sulfur dioxide tail gas drawn from the gas-liquid separator enters the drying tower for drying. The drying is filled with structured packing, and the acid divider is sprayed, with a spray volume of 30M 3 / h, drying acid temperature 40 ℃.
[0029] The dried sulfur dioxide tail gas is led to the mixer, and mixed with the pure oxygen from the oxygen system to form a mixed gas, so that the oxygen content increases from 10% to 20% (supplementing oxygen makes the oxygen content of the tail gas reach the normal oxygen content standard of air);
[0030] The mixed gas is sent to the fan, which is th...
PUM
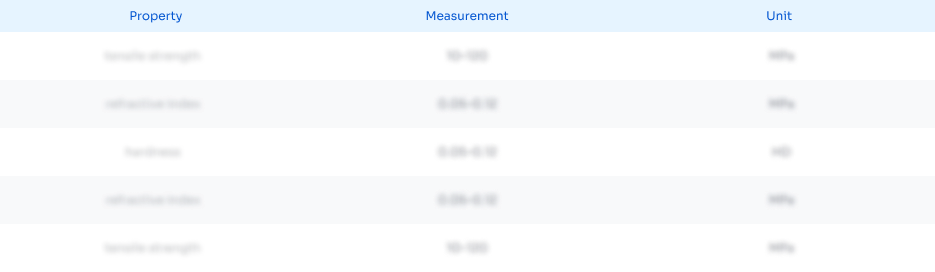
Abstract
Description
Claims
Application Information

- R&D Engineer
- R&D Manager
- IP Professional
- Industry Leading Data Capabilities
- Powerful AI technology
- Patent DNA Extraction
Browse by: Latest US Patents, China's latest patents, Technical Efficacy Thesaurus, Application Domain, Technology Topic, Popular Technical Reports.
© 2024 PatSnap. All rights reserved.Legal|Privacy policy|Modern Slavery Act Transparency Statement|Sitemap|About US| Contact US: help@patsnap.com