Aspirating type combined pulse detonation engine with secondary detonation
A detonation engine, combined pulse technology, applied in the direction of machine/engine, rocket engine device, mechanical equipment, etc., can solve the problem that the secondary detonation cannot be maintained for a long time, the amount of ejected air is limited, and the air supply is insufficient, etc. Insufficient oxidant, long detonation working time, favorable effect for successful transformation
- Summary
- Abstract
- Description
- Claims
- Application Information
AI Technical Summary
Problems solved by technology
Method used
Image
Examples
Embodiment 1
[0022] Such as figure 1 As shown, the air-breathing combined pulse detonation engine given in this embodiment includes a pre-detonation tube and a main detonation chamber.
[0023] Such as figure 2 As shown, the pre-detonator includes a pre-detonator head 7 , a pre-detonator detonation forming section 8 and a pre-detonator detonation propagation section 10 . The pre-explosion tube head 7 is a round tube with one end closed and one end open. The wall of the closed end of the pre-explosion tube head 7 is provided with a fuel inlet 1, an oxidant inlet 2 and an insulating gas inlet 3. The filling of the insulating gas is to prevent Premature ignition occurs, the oxidant and isolation gas enter the pre-explosion tube head 7 through the oxidant inlet 2 and the isolation gas inlet 3, the spark plug 5 is installed on the tube wall of the pre-explosion tube head 7, and the center of the installation position of the spark plug 5 is in line with the pre-explosion tube The distance of ...
Embodiment 2
[0031]Such as figure 1 As shown, the air-breathing combined pulse detonation engine given in this embodiment includes a pre-detonation tube and a main detonation chamber.
[0032] Such as figure 2 As shown, the pre-detonator includes a pre-detonator head 7 , a pre-detonator detonation forming section 8 and a pre-detonator detonation propagation section 10 . The pre-explosion tube head 7 is a round tube with one end closed and one end open. The wall of the closed end of the pre-explosion tube head 7 is provided with a fuel inlet 1, an oxidant inlet 2 and an insulating gas inlet 3. The filling of the insulating gas is to prevent Premature ignition occurs, the oxidant and isolation gas enter the pre-explosion tube head 7 through the oxidant inlet 2 and the isolation gas inlet 3, the spark plug 5 is installed on the tube wall of the pre-explosion tube head 7, and the center of the installation position of the spark plug 5 is in line with the pre-explosion tube The distance of t...
Embodiment 3
[0040] Such as figure 1 As shown, the air-breathing combined pulse detonation engine given in this embodiment includes a pre-detonation tube and a main detonation chamber.
[0041] Such as figure 2 As shown, the pre-detonator includes a pre-detonator head 7 , a pre-detonator detonation forming section 8 and a pre-detonator detonation propagation section 10 . The pre-explosion tube head 7 is a round tube with one end closed and one end open. The wall of the closed end of the pre-explosion tube head 7 is provided with a fuel inlet 1, an oxidant inlet 2 and an insulating gas inlet 3. The filling of the insulating gas is to prevent Premature ignition occurs, the oxidant and isolation gas enter the pre-explosion tube head 7 through the oxidant inlet 2 and the isolation gas inlet 3, the spark plug 5 is installed on the tube wall of the pre-explosion tube head 7, and the center of the installation position of the spark plug 5 is in line with the pre-explosion tube The distance of ...
PUM
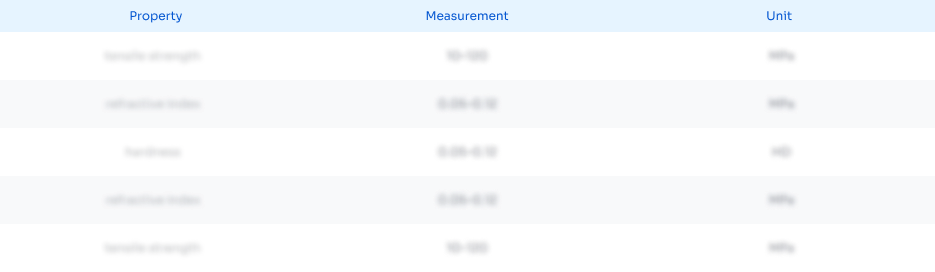
Abstract
Description
Claims
Application Information

- Generate Ideas
- Intellectual Property
- Life Sciences
- Materials
- Tech Scout
- Unparalleled Data Quality
- Higher Quality Content
- 60% Fewer Hallucinations
Browse by: Latest US Patents, China's latest patents, Technical Efficacy Thesaurus, Application Domain, Technology Topic, Popular Technical Reports.
© 2025 PatSnap. All rights reserved.Legal|Privacy policy|Modern Slavery Act Transparency Statement|Sitemap|About US| Contact US: help@patsnap.com