Method for identifying damage of aircraft structural parts based on acoustic emission detection
A technology for aircraft structural parts and acoustic emission detection, which is applied in the direction of material analysis using acoustic emission technology
- Summary
- Abstract
- Description
- Claims
- Application Information
AI Technical Summary
Problems solved by technology
Method used
Image
Examples
Embodiment
[0024] Taking the damage pattern recognition on a specific aircraft structural part as an example, the identification method provided by the present invention is illustrated below, and the specific steps are as follows:
[0025] Step 1. Place the acoustic emission sensor on the aircraft structure, and use vaseline as a coupling agent to make it in good contact;
[0026] Step 2. Place the sensors on the figure 2 at position (2) shown, image 3 At the positions (5) and (7) shown, stress is applied to the corresponding positions of the structural parts, so that the acoustic emission sensors respectively receive the deformation acoustic emission signals of the rivets on the structural parts, the acoustic emission signals generated by loose screws, and the crack propagation The acoustic emission signal is input to the acoustic emission signal processing system 4 through the preamplifier 3 for processing;
[0027] Step 3. Extract the characteristic parameters of the three acousti...
PUM
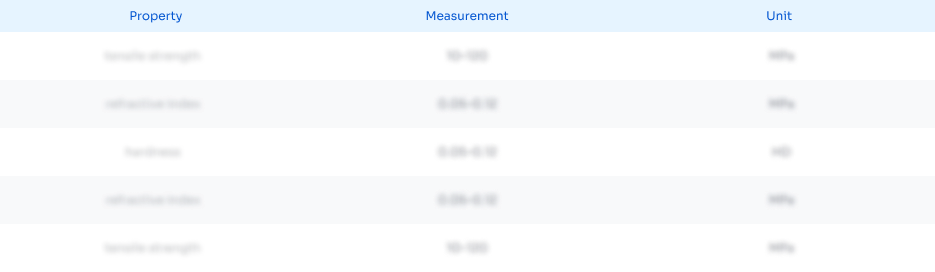
Abstract
Description
Claims
Application Information

- Generate Ideas
- Intellectual Property
- Life Sciences
- Materials
- Tech Scout
- Unparalleled Data Quality
- Higher Quality Content
- 60% Fewer Hallucinations
Browse by: Latest US Patents, China's latest patents, Technical Efficacy Thesaurus, Application Domain, Technology Topic, Popular Technical Reports.
© 2025 PatSnap. All rights reserved.Legal|Privacy policy|Modern Slavery Act Transparency Statement|Sitemap|About US| Contact US: help@patsnap.com