Permeability improvement technology for coal bed gas reservoir cap by using three-dimensional fracture network modification
A technology of coal bed methane and storage cap, applied in the direction of mining fluid, gas discharge, safety devices, etc., can solve the problems of prolonging the extraction time, failing to achieve the extraction effect, and increasing the gas permeability of coal storage caprock
- Summary
- Abstract
- Description
- Claims
- Application Information
AI Technical Summary
Problems solved by technology
Method used
Image
Examples
Embodiment 1
[0032] The thickness of the coal seam is 6 m, and the burial depth is 600 m. The soft and outburst coal seam 6 is nearly horizontal. The damage type of this seam is type IV or type V, and the coal body structure is mylonitic coal; the gas content is 25 m 3 / t, the gas pressure is 1.8 MPa; the coal seam roof 4 is medium sandstone and siltstone, 0.95-10.32m thick, with an average of 6.55m; the coal seam floor 7 is sandy mudstone or siltstone, with a thickness of 0.88-19.33 m, with an average of 7.00 m, There is a limestone aquifer on the floor of the coal seam, 20-30m above the coal seam, and the development of karst and fissures is uneven.
[0033] The implementation steps are as follows:
[0034] (1) Select a suitable location on the surface 1 and determine the well location;
[0035](2) Drill wells to the roof 4 and floor 7 of the coal seam with a three-shape shaft structure. Two horizontal wells 5 are constructed on the roof at an angle of 30°, and two horizontal wells 8 ...
Embodiment 2
[0039] For the soft, low-permeability, outburst coal seam 6 with a thickness of 8 m and a burial depth of 640 m, the failure type of this seam is Class IV, and the coal body structure is crushed coal; the gas content is 28 m 3 / t, the gas pressure is 1.9MPa; the coal seam roof 4 is sandy mudstone, 3.2-15.9m thick, with an average of 7.8m, and the coal seam floor 7 is siltstone, 2.6-17.6m thick, with an average of 7.6m. Unbalanced development of fissures.
[0040] The implementation steps are as follows
[0041] (1) Select a suitable location on the ground 1 and determine the well location;
[0042] (2) The horizontal well is constructed to the coal seam roof 4 and the coal seam floor 7 by adopting the three-shaft shaft structure. Firstly, the horizontal well constructed in the coal seam roof 4 has a diameter of 311.1 mm in the first opening hole 2 of the branch horizontal well, and is drilled into Φ244. 5mm N80 steel grade technical casing, the surface layer casing is open...
Embodiment 3
[0048] For the soft, low-permeability, outburst coal seam 6 with a thickness of 8 m and a burial depth of 640 m, the failure type of this seam is Class IV, and the coal body structure is crushed coal; the gas content is 28 m 3 / t, the gas pressure is 1.9MPa; the coal seam roof 4 is sandy mudstone, 3.2-15.9m thick, with an average of 7.8m, and the coal seam floor 7 is siltstone, 2.6-17.6m thick, with an average of 7.6m. Unbalanced development of fissures.
[0049] The implementation steps are as follows:
[0050] (1) According to the conditions and requirements of the roadway engineering, select the opening positions of drilling holes 9 and 10.
[0051] (2) Use a high-power drilling rig to construct a set of bedding-long drill holes 9 and 10 on the top plate 4 and bottom plate 7 of the working face, with a diameter of 120 mm and a depth of 200 m.
[0052] (3) The bedding-long drilling 9 of the top plate and the bedding-long drilling 10 of the bottom plate form an included a...
PUM
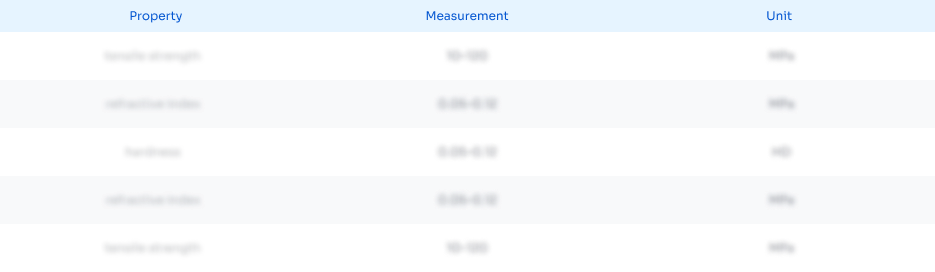
Abstract
Description
Claims
Application Information

- R&D Engineer
- R&D Manager
- IP Professional
- Industry Leading Data Capabilities
- Powerful AI technology
- Patent DNA Extraction
Browse by: Latest US Patents, China's latest patents, Technical Efficacy Thesaurus, Application Domain, Technology Topic, Popular Technical Reports.
© 2024 PatSnap. All rights reserved.Legal|Privacy policy|Modern Slavery Act Transparency Statement|Sitemap|About US| Contact US: help@patsnap.com