Optical epoxy resin and synthesis method thereof
A technology of epoxy resin and synthesis method, applied in the direction of organic chemistry, etc., can solve the problems of limited dosage, difficult dispersion of nanoparticles, and difficulty in popularization and application, and achieve the effects of good transparency, easy promotion and application, and moderate viscosity
- Summary
- Abstract
- Description
- Claims
- Application Information
AI Technical Summary
Problems solved by technology
Method used
Image
Examples
Embodiment 1
[0032] Add 0.25 moles of epichlorohydrin and 0.1 moles of dimercapto diphenyl sulfide into a three-necked flask equipped with a stirring device, a thermometer and a reflux condenser, stir and dissolve in a water bath; add 0.001 moles of quaternary ammonium salt as a catalyst ;React for 2 hours at a water bath temperature of 70°C; then raise the temperature, and recover most of the unreacted epichlorohydrin by distillation at a temperature lower than 120°C; then keep the reaction temperature at 70°C, and within 2~2.5 hours Add solid sodium hydroxide four times, adding once every 0.5 hours, wherein the total amount of sodium hydroxide added is 0.2 moles; then keep it warm for 0.5 to 1 hour at a temperature of 70°C to generate a reaction product. Add 0.2-2 moles of methyl isobutyl ketone into the reaction product, then stop stirring and discharge. Put the material in a separatory funnel, add 10 moles of distilled water, oscillate to form an organic layer and a water layer, separa...
Embodiment 2
[0035] Example 3
Embodiment 3
[0037] Example 4
PUM
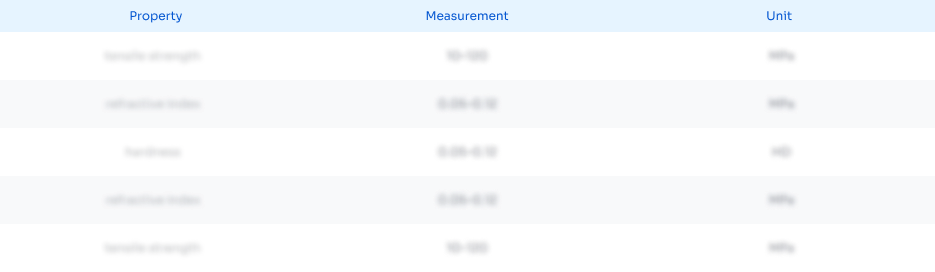
Abstract
Description
Claims
Application Information

- R&D Engineer
- R&D Manager
- IP Professional
- Industry Leading Data Capabilities
- Powerful AI technology
- Patent DNA Extraction
Browse by: Latest US Patents, China's latest patents, Technical Efficacy Thesaurus, Application Domain, Technology Topic, Popular Technical Reports.
© 2024 PatSnap. All rights reserved.Legal|Privacy policy|Modern Slavery Act Transparency Statement|Sitemap|About US| Contact US: help@patsnap.com