Paper feeding wheel and manufacturing method thereof
A manufacturing method and a technology of feeding rollers, applied in chemical instruments and methods, pile separation, layered products, etc., can solve the problems of affecting the surface friction of rubber wheels, reducing the surface friction of rubber wheels, and increasing process complexity, etc. Achieve the effect of simple manufacturing process, excellent wear resistance and easy demoulding
- Summary
- Abstract
- Description
- Claims
- Application Information
AI Technical Summary
Problems solved by technology
Method used
Image
Examples
Embodiment Construction
[0038] A method for manufacturing a paper feed wheel according to the present invention. The paper feed wheel is composed of a plastic skeleton 2 and a rubber wheel 1 sleeved thereon. Teeth 11, the rubber wheel 1 is formed by one-time compression vulcanization, and does not need to be ground again.
[0039] Described rubber wheel 1 is made of rubber composition, and this rubber composition comprises:
[0040] (1) Rubber with good wear resistance, which is a combination of butadiene rubber and natural rubber;
[0041] (2) A rubber vulcanization system, suitable for the butadiene rubber and natural rubber composition, which can fully vulcanize the rubber composition without causing surface blooming;
[0042] (3) At least one antioxidant, including at least one physical antioxidant, in addition to the antioxidant effect, it can also play a role in helping to release the rubber after vulcanization;
[0043] (4) At least one reinforcing filler, an appropriate amount of reinforcin...
PUM
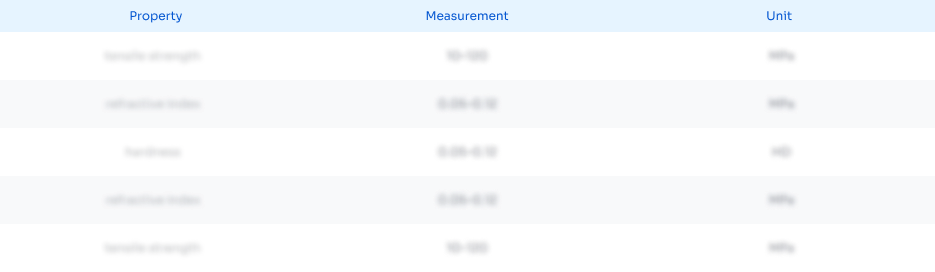
Abstract
Description
Claims
Application Information

- R&D
- Intellectual Property
- Life Sciences
- Materials
- Tech Scout
- Unparalleled Data Quality
- Higher Quality Content
- 60% Fewer Hallucinations
Browse by: Latest US Patents, China's latest patents, Technical Efficacy Thesaurus, Application Domain, Technology Topic, Popular Technical Reports.
© 2025 PatSnap. All rights reserved.Legal|Privacy policy|Modern Slavery Act Transparency Statement|Sitemap|About US| Contact US: help@patsnap.com