Layout method for 10 N thrusters of high orbit satellite platform
A thruster layout and satellite platform technology, which is applied in the direction of artificial satellites, aerospace vehicle propulsion system devices, etc., can solve the problems of too large difference between floor and back-floor thruster arms, low thruster working efficiency, large interference torque, etc. , to improve attitude control and orbit control performance, save propellant, and eliminate inter-axis coupling
- Summary
- Abstract
- Description
- Claims
- Application Information
AI Technical Summary
Problems solved by technology
Method used
Image
Examples
Embodiment Construction
[0017] In order to improve the ability to carry user payloads, it is necessary to improve the existing high-orbit satellite platform. The main changes are as follows: the height of the communication cabin is increased by 600mm, and the height of the service cabin remains unchanged. The height of the cylinder is increased to 4.40m. If the range of the center of mass from the beginning of life to the end of life is 1.96 to 1.84m, the distance between the docking surface of the star rocket and the geometric center is 2.20m, and the distance between the center of mass and the geometric center is 0.24 to 0.36m. The maximum difference in the distance from the back floor to the center of mass is 0.72m. After the height of the communication cabin increases, the installation positions of the north and south solar fins increase accordingly. In view of the need to install feeds and reflectors related to the east and west antennas in the upper middle of the east and west boards and the ad...
PUM
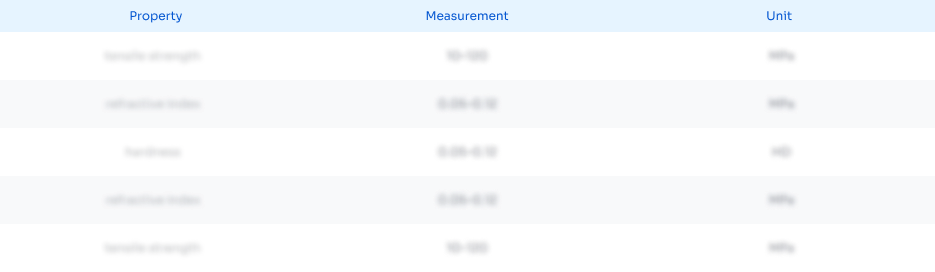
Abstract
Description
Claims
Application Information

- R&D Engineer
- R&D Manager
- IP Professional
- Industry Leading Data Capabilities
- Powerful AI technology
- Patent DNA Extraction
Browse by: Latest US Patents, China's latest patents, Technical Efficacy Thesaurus, Application Domain, Technology Topic, Popular Technical Reports.
© 2024 PatSnap. All rights reserved.Legal|Privacy policy|Modern Slavery Act Transparency Statement|Sitemap|About US| Contact US: help@patsnap.com