Rubber pipe molding mold and rubber pipe molding method
A technology for molding molds and molding methods, which is applied to household appliances, tubular objects, and other household appliances, and can solve problems such as non-recyclable, waste of resources, and environmental pollution caused by raw materials, and achieve the effect of avoiding waste of resources and environmental pollution
- Summary
- Abstract
- Description
- Claims
- Application Information
AI Technical Summary
Problems solved by technology
Method used
Image
Examples
Embodiment Construction
[0023] like figure 1 As shown, it is a schematic structural diagram of a rubber tube forming mold proposed by the present invention. Referring to the drawings, a rubber tube forming mold proposed by the present invention includes a forming core 1, a first positioning sleeve 2 and a second positioning sleeve 3, and the inner holes of the first positioning sleeve 2 and the second positioning sleeve 3 are steps The first positioning sleeve 2 is detachably sleeved on the upper end of the forming mold core 1, and the second positioning sleeve 3 is fixedly sleeved on the lower end of the forming mold core 1 by welding or screw connection. It should be noted that, the first positioning sleeve 2 is detachably sleeved on the forming die core 1 to ensure the operability of the rubber tube forming die.
[0024] The relative position between the first positioning sleeve 2 and the forming mold core 1 is fixed, which ensures that the first positioning sleeve 2 and the forming mold core 1 w...
PUM
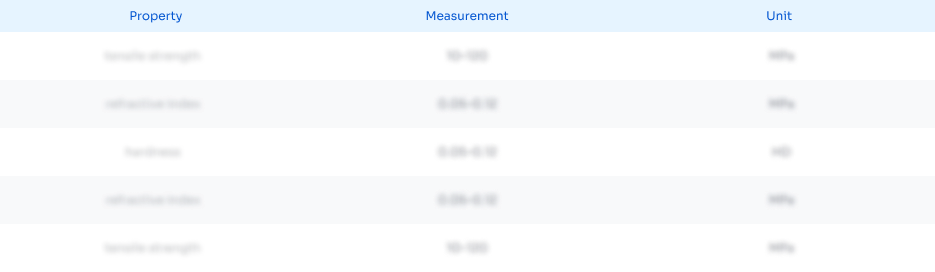
Abstract
Description
Claims
Application Information

- R&D
- Intellectual Property
- Life Sciences
- Materials
- Tech Scout
- Unparalleled Data Quality
- Higher Quality Content
- 60% Fewer Hallucinations
Browse by: Latest US Patents, China's latest patents, Technical Efficacy Thesaurus, Application Domain, Technology Topic, Popular Technical Reports.
© 2025 PatSnap. All rights reserved.Legal|Privacy policy|Modern Slavery Act Transparency Statement|Sitemap|About US| Contact US: help@patsnap.com