Encapsulation method for reducing vacuum leakage in composite material formation
A composite material and packaging method technology, applied in the field of composite material molding, can solve problems affecting the internal quality of composite materials, porosity or delamination defects in parts
- Summary
- Abstract
- Description
- Claims
- Application Information
AI Technical Summary
Problems solved by technology
Method used
Image
Examples
Embodiment 1
[0034] In this example, using figure 2 Encapsulated in the manner shown. Lay the carbon fiber / BMP316 polyimide resin prepreg on the mold, place the Bleader Lease E isolation cloth and Air Weave UHT800 air felt produced by AIRTECH in the United States in sequence, and then take the THERMALIMIDE vacuum bag as the packaging material to cover the carbon fiber / BMP316 polyimide resin prepreg, leave enough margin for the THERMALIMIDE vacuum bag, and paste it on the mold with the A-800-3G type sealing tape between the sealing groove of the inner ring first, so that the prepreg The material is sealed on the mold by the resin vacuum bag to form the first sealed space.
[0035] Take the Air Weave UHT800 air felt to cover the second air guide groove, and then paste the edge of the THERMALIMIDE vacuum bag on the mold with the outer ring A-800-3G sealing strip to form the second air guide groove between the inner ring seal groove and the outer ring seal groove. Sealed space. Open the s...
Embodiment 2
[0037] In this example, using figure 2Encapsulated in the manner shown. Lay the glass fiber / BMP350 polyimide resin prepreg on the mold, place the E5555 isolation cloth produced by American Richmond Company and the first-stage mat produced by Shanghai Fengya in sequence, and then take Richmond's VAC-PAKUHT-750 vacuum The bag is used as the packaging material to cover the glass fiber / BMP350 polyimide tree prepreg, leave enough margin for the VAC-PAK UHT-750 vacuum bag, and pass Richmond’s SM between the inner ring sealing groove first -5160 sealing tape is pasted on the mold, so that the prepreg is sealed on the mold by the VAC-PAK UHT-750 vacuum bag to form the first sealed space.
[0038] Take the first-stage felt to cover the second air guide groove, and then paste the edge of the VAC-PAK UHT-750 vacuum bag on the mold with the outer ring SM-5160 sealing strip to form the second air guide groove between the inner ring seal groove and the outer ring seal groove. Two sealed ...
PUM
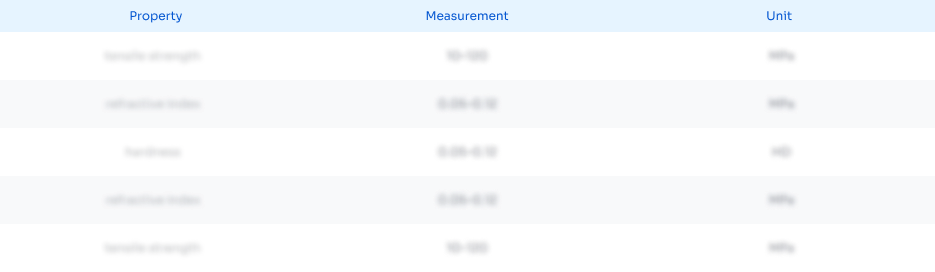
Abstract
Description
Claims
Application Information

- R&D
- Intellectual Property
- Life Sciences
- Materials
- Tech Scout
- Unparalleled Data Quality
- Higher Quality Content
- 60% Fewer Hallucinations
Browse by: Latest US Patents, China's latest patents, Technical Efficacy Thesaurus, Application Domain, Technology Topic, Popular Technical Reports.
© 2025 PatSnap. All rights reserved.Legal|Privacy policy|Modern Slavery Act Transparency Statement|Sitemap|About US| Contact US: help@patsnap.com