Method of soldering electronic component, and apparatus of same
An electronic component and welding method technology, which is applied in the field of electronic component welding and welding device, can solve the problems of time-consuming welding process, inability to control the amount of solder, etc., and achieve the effect of solving the residual solder
- Summary
- Abstract
- Description
- Claims
- Application Information
AI Technical Summary
Problems solved by technology
Method used
Image
Examples
Embodiment Construction
[0041] Hereinafter, preferred embodiments of the present invention will be described based on the drawings.
[0042] figure 1 A chip coil is shown as an example of the electronic component of the present invention. This chip coil 1 is formed by winding a coil 8 around a winding portion (not shown) of a magnetic core 2 , and the magnetic core 2 has flange portions 3 and 4 at both ends thereof. Both ends 8a, 8b of the coil 8 are drawn to the back side of the first flange portion 3 and drawn into two groove portions 3a, 3b formed at both ends of the back face of the flange portion 3 . Continuous electrodes 3c, 3d (indicated by oblique lines) are formed in the region from the bottom surface of these groove portions 3a, 3b to both end surfaces of the flange portion 3 . These electrodes 3c, 3d are welded to both ends 8a, 8b of the coil 8, respectively, as described below. exist figure 1 Here, the direction perpendicular to the mutual facing direction of the pair of electrodes ...
PUM
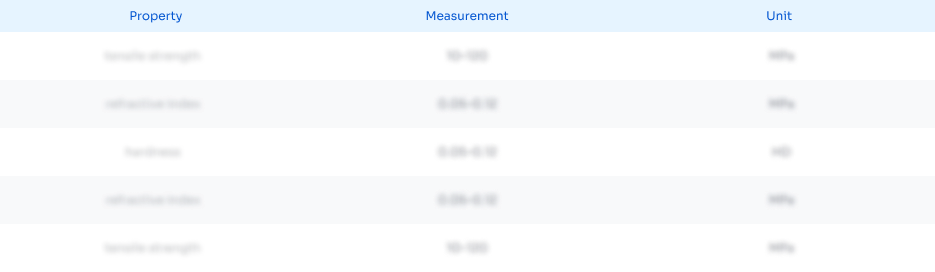
Abstract
Description
Claims
Application Information

- Generate Ideas
- Intellectual Property
- Life Sciences
- Materials
- Tech Scout
- Unparalleled Data Quality
- Higher Quality Content
- 60% Fewer Hallucinations
Browse by: Latest US Patents, China's latest patents, Technical Efficacy Thesaurus, Application Domain, Technology Topic, Popular Technical Reports.
© 2025 PatSnap. All rights reserved.Legal|Privacy policy|Modern Slavery Act Transparency Statement|Sitemap|About US| Contact US: help@patsnap.com