Method for machining composite components
A composite component, processing station technology, used in manufacturing tools, general control systems, program-controlled robots, etc.
- Summary
- Abstract
- Description
- Claims
- Application Information
AI Technical Summary
Problems solved by technology
Method used
Image
Examples
Embodiment Construction
[0029] in figure 1 For example, a rotor blade 10 is shown as a composite component to be processed. In the rotor blade 10 shown here, the rotor blade halves are directly bonded to each other. The resin overflows from the bonding seam in a manner not shown in detail here, so that a redundant part is generated here, which must be removed for further completion. To this end, the rotor blade 10 is fixedly clamped on the multi-part component holder 12. The clamped rotor blade 10 is surrounded by a plane door-shaped frame 14 in the working aisle, in which the door-shaped frame guide devices 16 are respectively arranged sideways. In the plane door frame 14, a processing tool 20 is provided on the lifting shaft 22.
[0030] Through the flat door-shaped frame 14, the processing head 20 with the installed processing tools can move along the composite component to be processed for processing the linear seam area.
[0031] in figure 2 with 3 The processing head 20 is shown in more detail i...
PUM
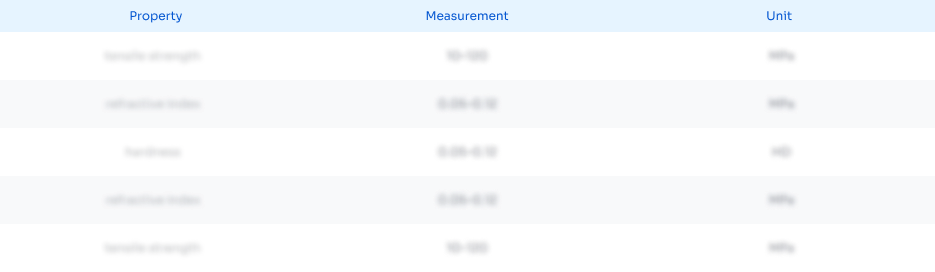
Abstract
Description
Claims
Application Information

- R&D
- Intellectual Property
- Life Sciences
- Materials
- Tech Scout
- Unparalleled Data Quality
- Higher Quality Content
- 60% Fewer Hallucinations
Browse by: Latest US Patents, China's latest patents, Technical Efficacy Thesaurus, Application Domain, Technology Topic, Popular Technical Reports.
© 2025 PatSnap. All rights reserved.Legal|Privacy policy|Modern Slavery Act Transparency Statement|Sitemap|About US| Contact US: help@patsnap.com