Mold and method for making multilayer plastic molded parts
A technology for molded parts and plastics, which is used in the field of manufacturing multi-layer plastic molded parts, and can solve the problems of inability to form back incisions, surface structural limitations, etc.
- Summary
- Abstract
- Description
- Claims
- Application Information
AI Technical Summary
Problems solved by technology
Method used
Image
Examples
Embodiment Construction
[0046] figure 1 An injection mold for producing a substrate is shown, consisting of a first mold half (1) and a second mold half (2). The base material is injected into the base material cavity (4) through the sprue (3). There are separate mold inserts (5) next to the substrate cavity side.
[0047] After the base material has reached a sufficiently high strength, the second half-mold (2) is replaced by the third half-mold (6) ( figure 2 ). The third mold half (6), the parting insert (5) and the hardened base material (7) now form the cavity (8) for the paint. An external parting agent may have to be applied to the inner surface of the mold half (6), but not to the parting insert. Through the gating system (9), lacquer is injected into the mold cavity to form the coating layer (8).
[0048] After the paint hardens, image 3 The illustrated coated components (moldings) can be demoulded. The molded part consists of a base material (7), a paint (10) and a side gate stub ...
PUM
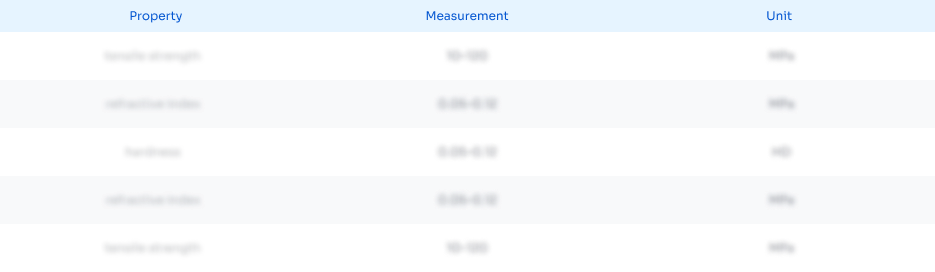
Abstract
Description
Claims
Application Information

- Generate Ideas
- Intellectual Property
- Life Sciences
- Materials
- Tech Scout
- Unparalleled Data Quality
- Higher Quality Content
- 60% Fewer Hallucinations
Browse by: Latest US Patents, China's latest patents, Technical Efficacy Thesaurus, Application Domain, Technology Topic, Popular Technical Reports.
© 2025 PatSnap. All rights reserved.Legal|Privacy policy|Modern Slavery Act Transparency Statement|Sitemap|About US| Contact US: help@patsnap.com