Internal and external molded wood-bamboo hollow plate and manufacturing method thereof
A manufacturing method and hollow board technology, which are applied in the direction of manufacturing tools, flat products, other household appliances, etc., can solve the problems of unreachable water absorption expansion rate, low longitudinal static bending strength, and no improvement, and improve the water absorption expansion rate, Improve sound absorption performance and eliminate the effect of broken boards
- Summary
- Abstract
- Description
- Claims
- Application Information
AI Technical Summary
Problems solved by technology
Method used
Image
Examples
Embodiment 1
[0085] ①Material preparation: process large-sized wood raw materials into shavings with a thickness of 1-3mm;
[0086] ② Drying: Dry the shavings to a moisture content of 3-8%.
[0087] ③Screening: Screen the shavings and scraps, and send the qualified raw materials with a thickness of 1-3mm, a length of 5-30mm, and a width of 1-10mm into the hollow board forming line;
[0088] ④Sizing: Apply glue evenly to the wood scraps, the adhesive is a liquid glue with a solid content greater than 52%, and the amount of glue is 6-10% of the weight of the wood scraps.
[0089] ⑤Extrusion molding: use a vertical extrusion machine with a hot-pressing temperature of 140-180°C to produce a formed hollow plate with a thickness of 28mm at a rate of 0.4-0.7m / min. Hollow plate cross-section selection Figure 14 The structure shown, using Figure 19 The extrusion head shown is extruded.
[0090] ⑥Post-processing: The produced hollow boards are cut into finished products with a specified format...
Embodiment 2
[0092] ①Material preparation: use bamboo shavings with a thickness of 1-3mm;
[0093] ② Drying: Dry the bamboo shavings to a moisture content of 3-5%.
[0094] ③Screening: Screen the bamboo shavings, and the qualified ones are sent to the hollow panel forming line.
[0095] ④Sizing: evenly sizing the bamboo shavings, the adhesive is a liquid glue with a solid content greater than 52%, and the sizing amount is 8-12% of the weight of the bamboo shavings.
[0096] ⑤Extrusion molding: A horizontal extrusion machine is used, the hot pressing temperature is 140-180°C, and the forming hollow plate with a thickness of 35mm is produced at a rate of 0.4-0.6m / min. Hollow plate cross-section selection Figure 13 The structure shown, using Figure 21 The extrusion head shown is extruded.
[0097] ⑥Post-processing: The produced hollow boards are cut into finished products with a specified format by the trimming machine.
Embodiment 3
[0099] ①Material preparation: Wheat straw scraps are used, and the length should be ≤30mm;
[0100] ② Drying: Dry the wheat straw scraps to a moisture content of 3-8%.
[0101] ③ Screening: Screen the wheat straw scraps, remove the long materials with a length greater than 30mm, and send the qualified ones to the hollow plate forming line.
[0102] ④ Glue sizing: evenly sizing the wheat straw scraps, the adhesive is a liquid glue with a solid content greater than 52%, and the sizing amount is 8-12% of the weight of the wheat straw scraps.
[0103] ⑤Extrusion molding: use a vertical extruder with a hot-pressing temperature of 140-180°C to produce a formed hollow plate with a thickness of 38mm at a rate of 0.4-0.5m / min. Hollow plate cross-section selection image 3 The structure shown, using Figure 20 The extrusion head shown is extruded.
[0104] ⑥Post-processing: The produced hollow boards are cut into finished products with a specified format by the trimming machine.
PUM
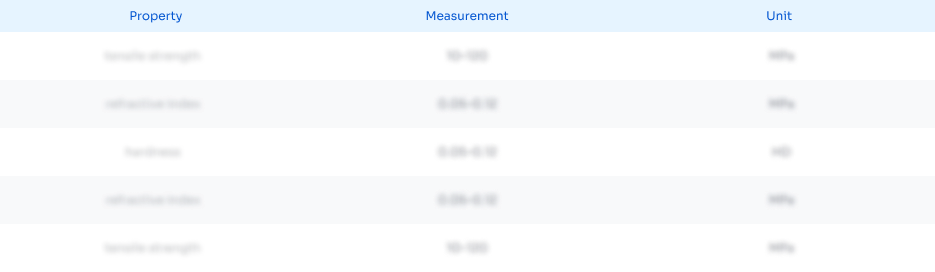
Abstract
Description
Claims
Application Information

- Generate Ideas
- Intellectual Property
- Life Sciences
- Materials
- Tech Scout
- Unparalleled Data Quality
- Higher Quality Content
- 60% Fewer Hallucinations
Browse by: Latest US Patents, China's latest patents, Technical Efficacy Thesaurus, Application Domain, Technology Topic, Popular Technical Reports.
© 2025 PatSnap. All rights reserved.Legal|Privacy policy|Modern Slavery Act Transparency Statement|Sitemap|About US| Contact US: help@patsnap.com