Branch three-leg five-DOF (degree of freedom) parallel mechanism containing double-compound drive
A technology of driving branches and degrees of freedom, applied in the field of robotics, can solve the problem of difficulty in obtaining precision dual macro and micro-drive parallel mechanisms, and achieve the effects of not easy interference, strong bearing capacity, and high dexterity.
- Summary
- Abstract
- Description
- Claims
- Application Information
AI Technical Summary
Problems solved by technology
Method used
Image
Examples
Embodiment 1
[0010] In the three-dimensional schematic diagram of Example 1, one end is connected to the machine base 1, and the other end is connected to the moving platform 2, and the two ends of the three branch chains are symmetrically distributed in an equilateral triangle, wherein the single drive branch chain is composed of two universal pairs 3-1, 3-2 and a driving and moving pair 4-1 form a branch chain of UPU series structure, the universal pair 3-1 is connected with the base, and the universal pair 3-2 is connected with the moving platform. The two universal joints are connected by a driving mobile joint, and the axis of the driving mobile joint passes through the centers of the universal joints at both ends. Each compound drive branch chain is composed of two rotating pairs 5, 6, a driving moving pair 4-2 and a spherical hinge 7, forming an RRPS type compound driving series structure branch chain, and the axes of the two rotating pairs intersect each other perpendicularly to for...
PUM
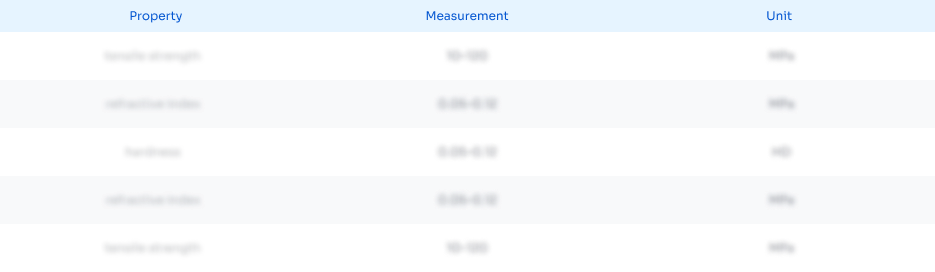
Abstract
Description
Claims
Application Information

- R&D
- Intellectual Property
- Life Sciences
- Materials
- Tech Scout
- Unparalleled Data Quality
- Higher Quality Content
- 60% Fewer Hallucinations
Browse by: Latest US Patents, China's latest patents, Technical Efficacy Thesaurus, Application Domain, Technology Topic, Popular Technical Reports.
© 2025 PatSnap. All rights reserved.Legal|Privacy policy|Modern Slavery Act Transparency Statement|Sitemap|About US| Contact US: help@patsnap.com