Blade root structure made of bamboo composite material and manufacturing method thereof
A blade root, composite material technology, applied in final product manufacturing, sustainable manufacturing/processing, wind turbines that are consistent with the wind direction, etc., can solve the problem of high cost of fan blades, increase the bonding area, improve bonding the effect of strength
- Summary
- Abstract
- Description
- Claims
- Application Information
AI Technical Summary
Problems solved by technology
Method used
Image
Examples
Embodiment Construction
[0064] The blade root structure and manufacturing method of the present invention will be further described in detail below in conjunction with the accompanying drawings and embodiments of the present invention.
[0065]At the blade root of the wind turbine, the part of the blade shell within 10 meters from the blade root includes at least bolt sleeves, glass fiber and bamboo, wherein the bamboo is in a long strip structure and arranged side by side, and the two adjacent bamboo strips The contact surfaces are parallel to each other, which can ensure that the fiber directions of all the bamboo strips are basically the same to jointly bear the blade load. Moreover, all or part of the connection between the glass fiber and the bolt sleeve and / or the strip-shaped bamboo is bonded as a whole by an adhesive in a miter joint, wherein the glass fiber and the bolt sleeve and / or Or between the long strips of bamboo and / or the foam wedge strips 12', a mitred joint can be used. The mitred...
PUM
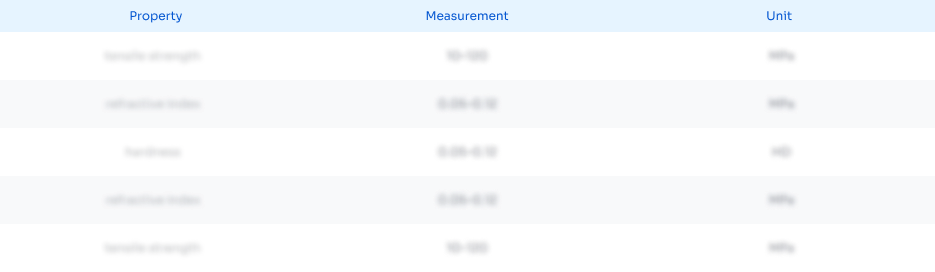
Abstract
Description
Claims
Application Information

- R&D
- Intellectual Property
- Life Sciences
- Materials
- Tech Scout
- Unparalleled Data Quality
- Higher Quality Content
- 60% Fewer Hallucinations
Browse by: Latest US Patents, China's latest patents, Technical Efficacy Thesaurus, Application Domain, Technology Topic, Popular Technical Reports.
© 2025 PatSnap. All rights reserved.Legal|Privacy policy|Modern Slavery Act Transparency Statement|Sitemap|About US| Contact US: help@patsnap.com