Multi-temperature sintering method for ceramic
A ceramic and high-temperature sintering technology, which is applied in applications, household utensils, clay products, etc., can solve the problems of insufficient pattern layers, large amount of colorant, discoloration, etc., and achieve the effect of rich color layers and bright colors
- Summary
- Abstract
- Description
- Claims
- Application Information
AI Technical Summary
Problems solved by technology
Method used
Image
Examples
Embodiment Construction
[0011] The present invention will be further described below in conjunction with the accompanying drawings and embodiments.
[0012] figure 1 It is a process flow chart of the new painted color firing method for special-shaped ceramics of the present invention.
[0013] See figure 1 , the multi-temperature firing method for ceramics provided by the invention comprises the following steps in turn:
[0014] Step S1: Select a fire-resistant ceramic body with a quartz sand percentage of less than 35% for pre-firing, remove moisture and organic impurities in the body, increase the surface strength of the body, and proceed to step S2;
[0015] Step S2: Pre-fire the colored glaze or transparent glaze at 800-1250°C for about 10 hours, and apply the colored glaze or transparent glaze on the surface of the embryo body. After the colored glaze or transparent glaze is pre-fired, it can avoid subsequent repeated high-temperature firings. Cracking and decolorization, enter step S3;
[0...
PUM
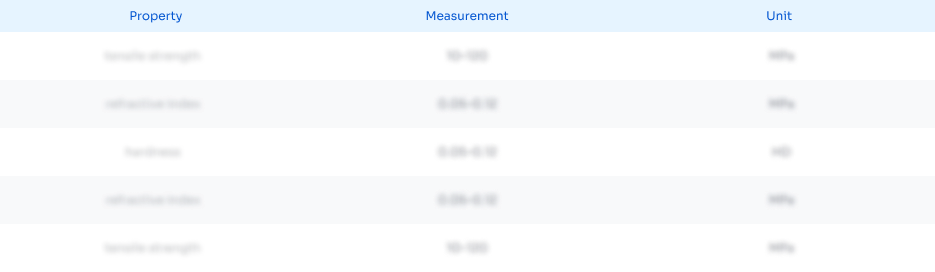
Abstract
Description
Claims
Application Information

- R&D
- Intellectual Property
- Life Sciences
- Materials
- Tech Scout
- Unparalleled Data Quality
- Higher Quality Content
- 60% Fewer Hallucinations
Browse by: Latest US Patents, China's latest patents, Technical Efficacy Thesaurus, Application Domain, Technology Topic, Popular Technical Reports.
© 2025 PatSnap. All rights reserved.Legal|Privacy policy|Modern Slavery Act Transparency Statement|Sitemap|About US| Contact US: help@patsnap.com