Rolling printing device for metal coil and rolling printing method for metal coil
A metal coil and coil technology, which is applied in the directions of printing devices, printing, printing machines, etc., can solve the problems of inability to realize continuous whole-roll substrate printing, inability to realize pattern printing, insufficient aesthetics, etc., and achieve good visual appearance and anti-counterfeiting. function, improve the shortcomings of sheet-fed flat printing, and fill in the effect of technical gaps
- Summary
- Abstract
- Description
- Claims
- Application Information
AI Technical Summary
Problems solved by technology
Method used
Image
Examples
Embodiment 1
[0018] refer to figure 1 , the metal coil printing device includes: a support 2, a coil substrate 1 is arranged on the support 2, and the coil substrate 1 moves on the support 2, and the movement of the coil substrate 1 can be carried out by various common driving parts Drive implementation; rotatable printing roller 3, the surface of the printing roller 3 is engraved with printing patterns, and the surface of the printing roller 3 is abutted against the coil substrate 1; it is used to add printing material to the printing roller 3 Material filling part 4. In this embodiment, the printing material filling part 4 includes a printing material tank 6 and a scraper 5, and the printing material in the printing material tank 6 is scraped onto the printing roller 4 by the doctor blade 5. The realization of this printing material filling part 4 The method is relatively simple, and the filling effect can meet the needs of basic production. The support member 2 includes a left support...
Embodiment 2
[0020] refer to figure 2 The printing material filling part 4 of this embodiment includes a printing material tank 6 and a bonding roller 7 , the bonding material roller 7 rotates in the groove of the printing material tank 6 , and the surface of the bonding material roller 7 is in close contact with the printing roller 3 . Compared with the first embodiment, this way of filling the printing material can achieve a relatively uniform filling effect, and the control of the rotation of the adhesive roller 7 is more convenient than the control of the scraper. The support member 2 of this embodiment includes an upper supporting roller 9 and a lower supporting roller 10 arranged vertically up and down and close to each other, and the coil substrate 1 is wound on the upper supporting roller 9 and the lower supporting roller in an "S" shape. 10, the arrangement of the upper support roller 9 and the lower support roller 10 allows the coil substrate 1 to pass between the two support ro...
Embodiment 3
[0022] refer to image 3 The printing material filling part 4 of the present embodiment includes a printing material tank 6, a bonding material roller 7 and a transfer roller 8, the bonding material roller 7 rotates in the groove of the printing material tank 6, and the surface of the transferring material roller 8 is respectively connected to the bonding material. Material roller 7 and printing roller 3 are close to each other. Compared with the second embodiment, the structure of this printing material filling part 4 increases the middle transfer roller 8, and the setting of the transfer roller 8 can further increase the uniformity of the printing material on the printing roller, and prevent the adhesive roller 7 from printing the material tank. 6 After the adhesive is applied, it is directly coated on the printing roller 3 without treatment. Regarding the arrangement of the supporting member and the printing roller, this embodiment adopts the same setting method as that of...
PUM
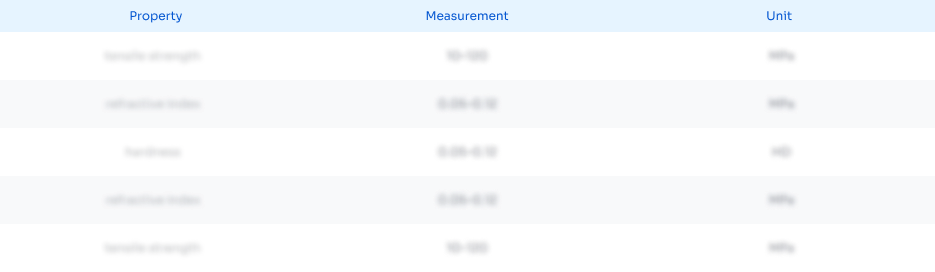
Abstract
Description
Claims
Application Information

- R&D Engineer
- R&D Manager
- IP Professional
- Industry Leading Data Capabilities
- Powerful AI technology
- Patent DNA Extraction
Browse by: Latest US Patents, China's latest patents, Technical Efficacy Thesaurus, Application Domain, Technology Topic, Popular Technical Reports.
© 2024 PatSnap. All rights reserved.Legal|Privacy policy|Modern Slavery Act Transparency Statement|Sitemap|About US| Contact US: help@patsnap.com