Differential motion airtight feeding electric furnace smelting device and feeding method thereof
A technology of electric furnace smelting and feeding equipment, which is applied in the field of metallurgy, can solve the problems of dioxin emissions that cannot meet environmental protection indicators, reduce transmission power, and laying thickness can not be too large, so as to reduce equipment maintenance and auxiliary energy consumption, reduce Dust content, discharge temperature, and the effect of reducing the probability of generation of harmful components
- Summary
- Abstract
- Description
- Claims
- Application Information
AI Technical Summary
Problems solved by technology
Method used
Image
Examples
Embodiment Construction
[0061] The present invention will be described in detail below in conjunction with the accompanying drawings, as shown in the figure: the electric furnace smelting device for differential airtight feeding in this embodiment includes an electric furnace 1 and a charging device, and the charging device includes a cold receiving conveying tank 2 and a hot conveying trough 3, an independently controlled vibration excitation device I4 is provided under the cold receiving material delivery tank 2, an independently controlled vibration excitation device II5 is provided under the hot delivery tank 3, and an extension into the conveying throat 6 in the heat conveying trough 3, the distance between the conveying throat 6 and the bottom of the heat conveying trough 3 is equal to or greater than the depth of the heat conveying trough 3, the distance between the cold receiving conveying trough and the hot conveying trough space The height difference makes the vibration excitation device Ⅰ a...
PUM
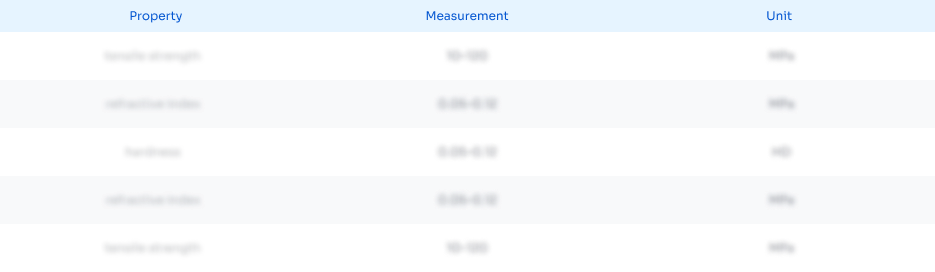
Abstract
Description
Claims
Application Information

- R&D
- Intellectual Property
- Life Sciences
- Materials
- Tech Scout
- Unparalleled Data Quality
- Higher Quality Content
- 60% Fewer Hallucinations
Browse by: Latest US Patents, China's latest patents, Technical Efficacy Thesaurus, Application Domain, Technology Topic, Popular Technical Reports.
© 2025 PatSnap. All rights reserved.Legal|Privacy policy|Modern Slavery Act Transparency Statement|Sitemap|About US| Contact US: help@patsnap.com