Die for strips of winding pipes
A technology for winding pipes and strips, which is used in the field of molds for manufacturing plastic-steel winding pipes and strips, can solve problems such as product defects and unreasonable flow channel structures, and achieve the effects of sufficient material supply, sufficient material supply, and complete structural formation.
- Summary
- Abstract
- Description
- Claims
- Application Information
AI Technical Summary
Problems solved by technology
Method used
Image
Examples
Embodiment 1
[0033] like Figure 2 to Figure 7 As shown, the coiled pipe strip mold of the present invention includes an upper cover plate 21, a core plate, a runner plate 24, a transition plate and a discharge plate, and the core plate, the transition plate and the discharge plate are along the feed direction of the mold steel band 80 Connect sequentially.
[0034] The upper cover 21 includes a molten plastic injection port 211 connected to the molten plastic feed pipe 50 .
[0035] The core plate includes an upper core plate 22 and a lower core plate 23 that are connected up and down. The upper core plate 22 is connected with the upper cover plate 21 up and down. The upper core plate 22 includes a runner groove 221 located below the molten plastic injection port 211 .
[0036] The core plate includes core plate steel strip guide holes 100 arranged at the same level in parallel intervals, a runner lower slope 200 inclined downward along the mold steel strip feeding direction, and an inn...
Embodiment 2
[0058] like Figure 8 As shown, the coiled pipe strip mold of the present invention includes an upper cover plate 21, a core plate, a runner plate 24 and a discharge plate. The difference between this embodiment and Embodiment 1 is that the transition plate is cancelled, and the discharge plate is directly connected to the discharge end of the core plate. The tape is compounded with molten plastic only once. One end of the auxiliary runner channel 242 arranged on both sides of the runner plate 24 communicates with the runner groove 221 , and the other end communicates with the cavity of the overlapping edge arranged on the discharge plate.
Embodiment 3
[0060] On the mold core of the existing coiled pipe strip mold adopting the formwork structure, the auxiliary runners located on both sides of the main flow channel and connected to the groove of the flow channel and the cavity of the lap edge of the strip can also be realized. .
PUM
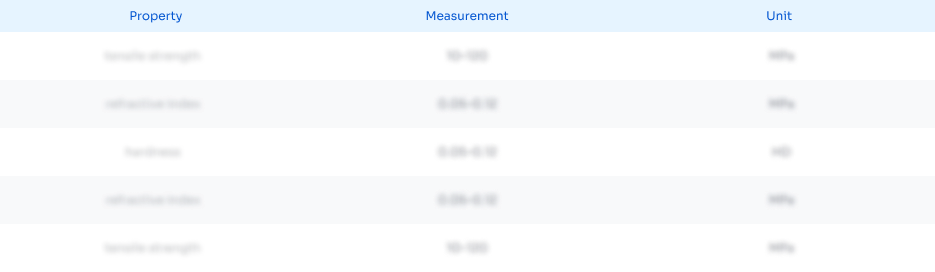
Abstract
Description
Claims
Application Information

- R&D
- Intellectual Property
- Life Sciences
- Materials
- Tech Scout
- Unparalleled Data Quality
- Higher Quality Content
- 60% Fewer Hallucinations
Browse by: Latest US Patents, China's latest patents, Technical Efficacy Thesaurus, Application Domain, Technology Topic, Popular Technical Reports.
© 2025 PatSnap. All rights reserved.Legal|Privacy policy|Modern Slavery Act Transparency Statement|Sitemap|About US| Contact US: help@patsnap.com